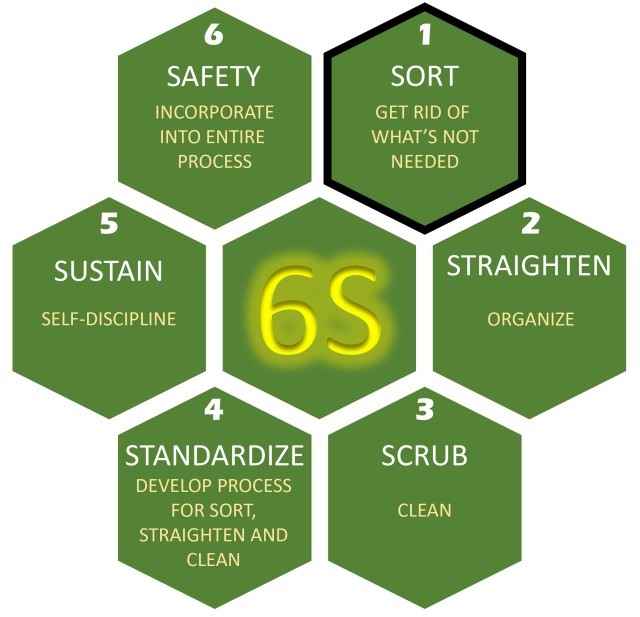
ANNISTON ARMY DEPOT, Ala. -- Most folks associate 6S with housekeeping.
To a degree, this is accurate, but it also includes organization and efficiency – “A place for everything and everything in its place.”
6S applies to every part of our installation, including offices, shops, conference rooms, break rooms and even bathrooms.
Henry Ford introduced the 5S concept into manufacturing. He called it CAN DO (Clean-up, Arrange, Neatness, Discipline, On-going).
While the names are not the same, the concept he developed is the basically same as the 6S (Sort, Straighten, Scrub, Standardize, Sustain, Safety) process from the Toyota Production System, with the exception of the emphasis on safety.
Each S is worked in sequential order, with the exception of safety, which is a key component in each S.
A good 6S process is essential to our continuous process improvement initiative.
Each S will be addressed in six separate articles in an attempt to better distinguish between each phase. This first article deals with sort.
Sort – what is needed and what is not
The short definition of sort is to get rid of what’s not needed.
Many times, while working through the 6S process, we look at sort on the surface.
The intent of true sorting involves a complete declutter. We must take everything in the work area into consideration, including tools, furniture, supplies, equipment, books, documents, bulletin board material, drawers, supply cabinets, shelves – everything.
Arrange for removal and proper disposition of the items you definitely do not need.
For the items that may or may not be needed, place a red tag on them and remove them from the immediate work area until a determination can be made. Set a reasonable time limit and stick to it to determine what to do with the material.
Coordinate with everyone having a vested interest in the material, to ensure the right decision is made.
Once a decision is made, follow through.
Remember the key to being able to sustain the sort part of the equation is following through with the remaining Ss. Otherwise, you will not have controls in place to prevent the clutter from returning.
Social Sharing