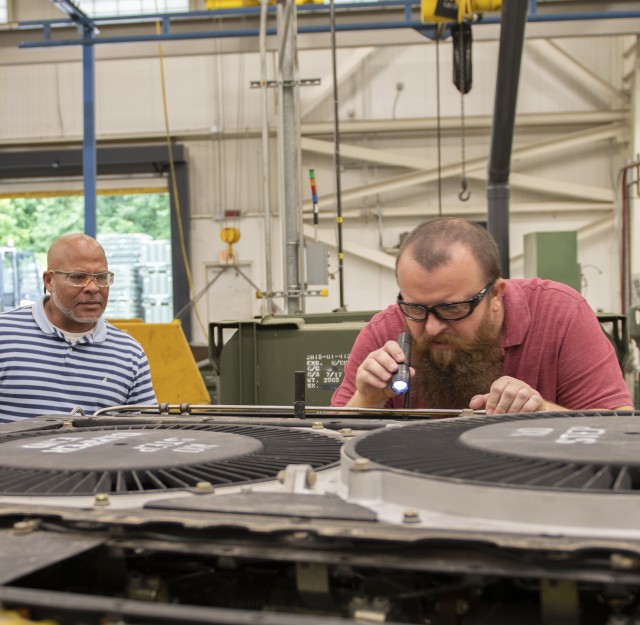
ANNISTON ARMY DEPOT, Ala. -- The external Product Quality Deficiency Report process is one way Anniston Army Depot receives feedback from customers.
Through this process, the customer submits a PQDR into the Product Data Reporting and Evaluation Program.
Here at ANAD, the PQDR coordinator, reviews and filters the PQDR written against ANAD, determining its validity, then forwards the information to the supervisor in the area where the component, vehicle or weapon was produced, along with a 702-10-E form. After evaluation, this form will state the findings for the final reply to the customer.
Once the deficient product arrives at ANAD, the shop supervisor works with the quality inspector and a subject matter expert in that area to determine the cause of the deficiency. Photos substantiate the findings.
“Basically, they study it and find out what is wrong with the product and report on it,” said Fred Hunter, the depot’s PQDR coordinator.
Once the inspection is complete, the supervisor fills out their portion of the 702-10-E form, and the PQDR coordinator prepares the final reply.
The entire process, from the initial deficiency report through the reply to the customer, should take 30 to 60 days, depending on the situation.
“The biggest problem the PQDR process has, is shipping and receiving,” said Hunter, adding that when an item arrives on depot, it isn’t always immediately routed to the location where it needs to be inspected.
The Quality Assurance Office is currently working on a method to correct that issue and develop a better receiving process for defective material.
“There should be a centrally located receiving point for all external PQDR shipments in the future,” said Hunter.
Following inspection, there are four determinations, which can be made:
• Valid-internal: A customer complaint, determined through internal investigation, to be the responsibility of ANAD.
• Valid-external: A customer complaint, determined through internal investigation as a valid complaint, not to be the responsibility of ANAD.
• Invalid: A customer complaint, determined through internal investigation, to be invalid. These complaints result from, but are not limited to: customer expectations exceeding material/component capability, user expectations exceeding overhaul requirements, material damaged/neglected by the user or no evidence of failure.
• Information: A PQDR that is for informational purposes only. No replacement or credit exchanged
Often, the result of the PQDR is not an issue created by ANAD employees, but the parts used during repair or overhaul.
“It’s not always so much our workmanship that cause the PQDR. It’s often faulty components, which is something ANAD cannot control,” said Hunter.
Between 2017 and 2019, there were 299 PQDRs sent to ANAD.
Of those, 32 were determined to be ANAD’s responsibility.
More than 47 percent were invalid and approximately 36 percent were valid-external complaints.
No matter the cause of the problem, making it right for the customer is important to ANAD.
A review of internal processes is one benefit stemming from all PQDRs, according to Mark Lashall, chief of the Vehicle Quality Branch.
“It prompts us to look at our processes and, potentially, improve them,” said Lashall. “It gives our quality assurance specialists throughout the shops feedback and the inspectors in the shops may increase inspections for a while.”
One area, according to Lashall, where this has had an impact is in production of reciprocating engines.
A large number of PQDRs a few years ago resulted in increased quality checks throughout the engine overhaul process.
“We’ve been able to improve our processes, whether there was an issue or not,” he said.
Social Sharing