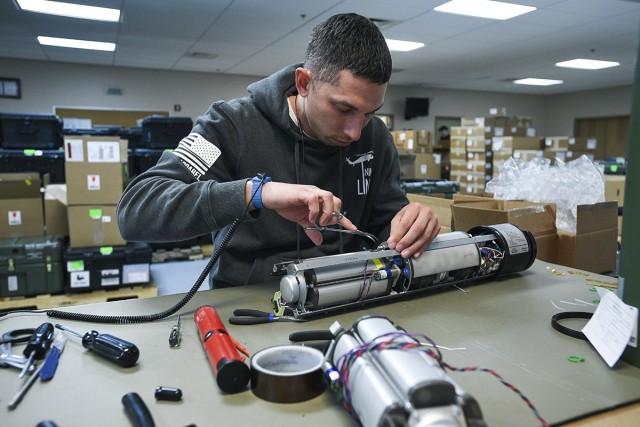
FORT DETRICK, Md. -- U.S. Army Medical Logistics Command is requiring all units with portable oxygen generators to report their maintenance compliance status and concurrently execute a required preventive maintenance check on services on their devices.
Status reports should be made immediately through the Modification Management Information System (MMIS) in the AESIP Army Enterprise.
The Oxygen Generator Field Portable, or OGFP (Model: 3000, NSN: 3655-01-648-5957, LIN: P05027), is vulnerable to damage from humidity and other sources of moisture, which can degrade performance or require repairs, according to the directive issued by AMLC’s Medical Maintenance Policy and Analysis (M2PA) directorate.
The most susceptible component is the Advanced Technology Fractionator (ATF), a module within the device through which the incoming air passes. Moisture can cause the ATF’s molecular sieve, a material with tiny pores that blocks certain larger molecules while allowing smaller ones to pass, to lose its ability to perform gas separation resulting in the OGFP’s inability to produce oxygen to purity specifications, according to the directive.
If this malfunction occurs, the device will need to be returned to a U.S. Army Medical Materiel Agency Medical Maintenance Operations Division for a depot-level repair.
“This isn’t a device flaw. This is about maintenance,” said Chief Warrant Officer CW5 Jesus Tulud, director of M2PA. “The likelihood of ATF damage can be reduced by strictly following the manufacturer’s recommendations for periodic services and routinely running the OGFP.”
On a monthly basis, operators should turn on a full-charged OGFP and let the device run until the power is fully drained, which takes approximately 30 minutes. It is highly recommended to do so “especially in humid or non-climate controlled environments or storage locations.”
Failure to adhere to manufacturer’s recommendations can lead to increased downtime, including the need for a depot-level repair. The OGFP can be found in numerous medical materiel sets, such as the ground ambulance, air ambulance and forward resuscitative and surgical team sets.
AMLC has released an equipment fact sheet to help units better understand how to properly maintain the device. It can be found here.
When units report their maintenance compliance via MMIS, the system utilizes a centralized database to facilitate automated, web-based message processing. In this capacity, it serves the Army’s coordinated process for development, application and documentation of hardware and software changes that are made to end items, components and information systems based on publication of Modification, Safety and Class VIII message requirements. This system assists users in determining the status of equipment end item and component modifications at the Serial Number (SN) level as well as non-serialized pharmaceuticals, vaccines and medical supplies.
MMIS is available through the AESIP Army Enterprise for account holders with Internet access, a .mil e-mail address, a Secret security clearance and an ability to login using a Common Access Card (CAC). Learn more here.
Questions about this maintenance action directive can be forwarded to the M2PA team at usarmy.detrick.medcom-usamma.mbx.m2pa@mail.mil or by phone at 301-619-8578 (DSN: 312-343-8578).
Social Sharing