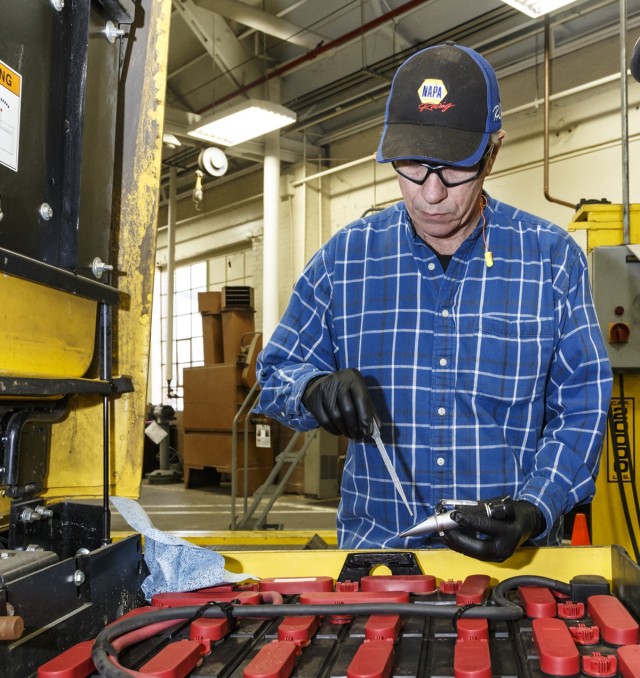
ANNISTON ARMY DEPOT, Ala. -- Five teams comprised of a mixture of supervisory and non-supervisory employees at Anniston Army Depot have been assisting the Safety Office with information and implementation of the depot’s Occupational Safety and Health Administration Challenge program for the past seven months.
One of those teams, the Safety and Health Training Committee, has been tasked with training recommendations and performing audits to verify the training was performed and was effective.
Employees may see them in the shops performing two types of audits – one for new hires and one for existing employees.
The new hire audits are performed twice – once when the employee has been in their work area for 30 days and again 90 days after their hiring date.
“We started by targeting new employees following their New Employee Orientation,” said Jeremy Boling. “The purpose behind these audits is to make sure employees receive the proper safety training before they get their boots on the ground, so to speak, on the shop floors.”
As of early March, almost 60 new employees had been surveyed.
During the audits for existing employees, the team looks to learn how safety can be improved in various work areas and whether or not employees are being trained correctly.
Boling said those audits essentially check for complacency – ensuring employees and supervisors aren’t presuming they know the content of the training already.
“Complacency can be one of our biggest safety threats, in my opinion,” said Boling.
During these audits, they also ask if employees are being cross-trained and what training they receive if they are moved to another shop or work on a different process.
“Without honest employee feedback, we don’t know what is happening on the shop floor,” said Boling.
According to Juston Daniel, the committee often request additional employees from throughout the depot to assist with the surveys.
In January and February, employee teams, each comprised of about 10-12 employees, were tasked to survey at least 100 employees each time they were sent to shop floor areas.
“From late November until mid-March, our team was able to bring safety awareness to almost 300 employees. Our team is on pace to reach roughly 1,100 employees by the end of August, which would be about 36 percent of the workforce,” said Daniel.
The results of each audit are given to the Safety Office.
Social Sharing