Working with munitions is an inherently dangerous business. As the primary manager of ammunition and explosive materials for the US military, U.S. Army Joint Munitions Command takes pride in its consistent commitment to safety. JMC’s focus continues to be rewarded at both the command and installation level. The Secretary of the Army and Chief of Staff of the Army recognized JMC as winner of the Army Exceptional Organization Safety Award for FY18, and Anniston Munitions Center won the FY19 Army Materiel Command Excellence in Explosives Safety Award.
According to Luke Kearns, JMC Safety Division, “In order to provide lethality that wins, JMC must ensure the safety of both its Soldiers and Civilians. This recognition highlights our JMC Headquarters' commitment and our safety staff's efforts. This is an important part of ensuring a resilient and professional workforce executing and promoting the JMC mission.” Such success comes from JMC’s commitment to continuous improvement in explosives safety.
Ammunition and explosives safety have been issues since the founding of the Army. For the first century and a half, Army regulations concerning the manufacture, storage and handling of ammunition and explosives were sparse. This was due the way the Army procured munitions. During the American Revolution, gunpowder production was decentralized, resulting in inconsistent production, loose safety standards and frequent shortages. The Army developed Arsenals during the War of 1812 and the Civil War, but relied on munitions contractors for gunpowder. Thus, the Army played little role in regulating explosives safety.
By the 20th century, the United States lacked a strong peacetime munitions industry. The World War I approach was to convert existing American industries into war production facilities, leading to inconsistencies in safety. Despite the conversion of hundreds of facilities, the United States still relied on European sources for most of its munitions requirements.
Early improvements in safety often came in response to explosions. In 1914, a committee of the Association of Manufacturers of Powder and High Explosives conducted a study of 122 explosives-related accidents since 1864. As a result, the group established the American Table of Distances, which set minimum distances occupied buildings and explosives facilities. Despite this improvement, munitions-related accidents continued, with hundreds killed in explosions at New Jersey and Pennsylvania facilities between 1917 and 1924. In 1926, a lightning-caused explosion at Lake Denmark led to the formation of what became the Department of Defense Explosives Safety Board and the start of construction of Hawthorne Naval Ammunition (now Hawthorne Army Depot) in 1928.
On the eve of World War II, a combination of military and public facilities could only produce 5 percent of the U.S. military’s munitions requirements. This led to the construction of 60 dedicated manufacturing facilities by the end of the war, all operated by contractors. Greater military involvement saw the adoption of more consistent safety regulations across the munitions industrial base. In particular, the procurement of large tracts of land for each installation made it possible for production lines to be spaced out and distant from other structures. Despite these efforts, safety standards varied between the 2,400 contractors and 20,000 subcontractors producing munitions by the end of the war. This contributed to 667 munitions-related fires and explosions during World War II, resulting in 300 fatalities. In 1947, at Texas City, 2,000 tons of ammonium nitrate exploded, resulting in 600 fatalities and prompting the Army to establish improved safety standards.
New regulations revised the numbers established in the American Table of Distances, set explosives limits for facilities and developed Explosive Safety Site Plans. JMC relies heavily on ESSPs, which are regularly revised to ensure the safe placement and operation of explosives-related sites, including manufacture, testing, storage, and demilitarization. In addition, each JMC installation or activity with an ammunition mission maintains an Explosives Safety Management Program. ESMPs receive annual evaluation, with locations housing larger explosives missions evaluated more frequently.
JMC’s installations reflect high standards for safety in a variety of ways. In February 2019, Anniston Munitions Center demilitarized 700,000 sub-munitions, using a robotic system that keeps people out of harm’s way.
“This is exactly the kind of thing to use robotics for — to get humans out of harm's way,” said Bill Prentice, a lead computer scientist for the project. “Let the automation of robots do what they do well, and have humans make advanced decisions on safety.”
In December, Blue Grass Army Depot reopened critical work areas after replacing an outdated portable firefighting system with an overhead water deluge system. The new method responds to a spark or flash within 50 milliseconds to flood work areas, another critical step toward using technology to reduce human contact with dangerous situations.
JMC extends its safety focus to environmental concerns, as well. For nearly two decades, Crane Army Ammunition Activity has improved safety by using a closed system process for the environmentally-friendly destruction of unusable materials, particularly the demilitarization of ammonium picrate. Commonly known as Yellow D, ammonium picrate is toxic, flammable and can easily contaminate water sources. Due to its fine consistency, Yellow D cannot be disposed of via open burning or open detonation. Crane AAA partners with contractor Gradient Technology to convert ammonium picrate to ammonium nitrate and
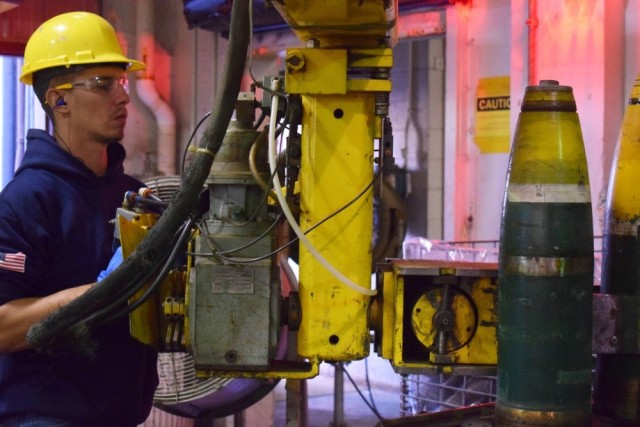
picric acid.
Social Sharing