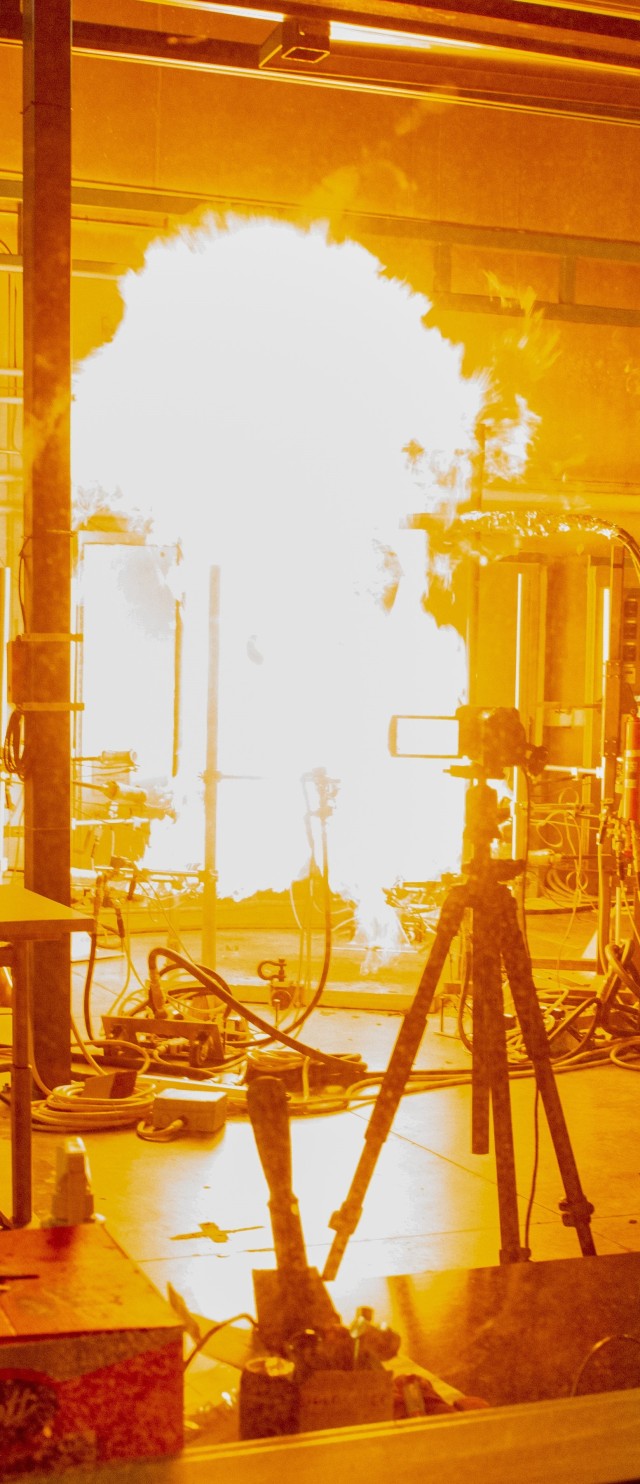
NATICK, Mass. -- A new burner system is improving testing capabilities at the U.S. Army Combat Capabilities Development Command Soldier Center, making testing even more consistent and precise.
The CCDC Soldier Center is dedicated to using science and technology to ensure America's warfighters are optimized, protected, and lethal. CCDC SC supports all of the Army's Modernization efforts, with the Soldier Lethality and Synthetic Training Environment Cross Functional Teams being the CCDC SC's chief areas of focus. The center's science and engineering expertise are combined with collaborations with industry, DOD, and academia to advance Soldier and squad performance. The center supports the Army as it transforms from being adaptive to driving innovation to support a Multi-Domain Operations Capable Force of 2028 and a MDO Ready Force of 2035. CCDC SC is constantly working to strengthen Soldiers' performance to increase readiness and support for warfighters who are organized, trained, and equipped for prompt and sustainable ground combat.
Experts at the CCDC Soldier Center perform thermal and flame-resistance testing on Soldier protective garments and other equipment to analyze effectiveness and possible degradation over time.
The new burners are part of the Ouellette Environmental Protection Test Facility at CCDC SC, which tests clothing and equipment materials for service members, first-responders and members of law enforcement. The facility, which is part of the Soldier Protection and Survivability Directorate, features evaluation and analysis labs and a propane test cell, where flash-fire testing previously done with eight burners on a full-scale thermal test manikin is now done with the new 12-burner system, allowing for a more even distribution of heat.
"The new burner system allows us to adjust the pressure to regulate the heat flux on the manikin and to work across a variety of environmental conditions and still achieve the proper heat flux without having to move the burners closer or farther out," said Cheryl Stewardson, a physical scientist in the Soldier Center Environmental Protection Test Facility. "This also provides consistency between burns on the same day as well as week to week and month to month. Consistency is key to standardized testing to provide repeatable and reliable test results to our customers."
The new burner system was truly a Team Natick effort.
"The burners were designed by Mike Grady in our electronics shop, who partnered with our machine shop to do all the cutting and welding," said Stewardson. "Mike then did the final production of wiring the solenoids and igniters. He also worked with an on-site contractor, who helped with the propane fittings and lines. The system connects to a control system developed by our engineering cell. Everyone was great contributing their expertise and talents."
Stewardson explained that the flame manikin test, known as ASTM F1930, provides a system-level view of how a flame-resistant garment will respond and protect in a flash-fire scenario. The new burner system supports the ASTM F1930 testing, which plays an important role in ensuring the quality and reliability of items for the warfighter.
"It's one thing to test fabric swatches, and another to test the full garment," said Stewardson. "Testing here allows project engineers to see how all of the materials and the design of the system affect flammability and the potential for burn injury, both in the early stages of development, and throughout the lifespan of the item. It also provides the Product Manager with insights to how engineering change proposals might affect the performance of the garment, and to ensure that production and inventory remains consistent in performance."
The Soldier Center supports several organizations with the testing, including Product Manager Soldier Clothing and Individual Equipment (PM SCIE) -- which is part of Program Executive Office Soldier (PEO Soldier), the Navy Clothing and Textile Research Facility (NCTRF), Product Manager Soldier Protective Equipment (PM SPE), Marine Corps Systems Command (MARCORSYSCOM), Naval Air Systems Command (NAVAIR), Naval Sea Systems Command (NAVSEA), PM Special Operations Forces (SOF) Survival Systems, Joint Project Manager for Protection (Joint PM-Protection), and the U.S. Air Force Uniform Office (AFUO).
A recent effort involved routine quality assurance testing for the PM SCIE Quality Team. The testing simulated a fuel flash fire using the new 12-burner system. Part of the purpose of the testing was to create a baseline for new items to make sure that they are not degrading over time.
The testing was performed on the Flame-Resistant Army Combat Uniform, the Army Combat Shirt/Army Combat Pant, the Improved Combat Vehicle Coverall, and the Army Aircrew Combat Uniform.
"Product Manager Soldier Clothing and Individual Equipment conducts monthly quality assurance surveillance testing for our flame-resistant clothing items to ensure that they meet the requirements of the specification and the Capabilities Production Document (CPD) and that this performance does not degrade over time," said Susan McLendon, Quality Assurance Team Lead, PM SCIE. "We also test to have a baseline for current flame-resistance protection to serve as a reference to evaluate new products."
The Soldier Center's testing expertise and facilities play an essential role in ensuring that Soldiers are protected.
"It is important to do continual testing of the FR garments to ensure they maintain the protection level for flash-flame incidents," said Stacey Lee, a project engineer in the Soldier Protection and Survivability Directorate who provides matrixed support to PM SCIE.
"It is critical that the testing is accurate and repeatable over time," said McLendon.
Social Sharing