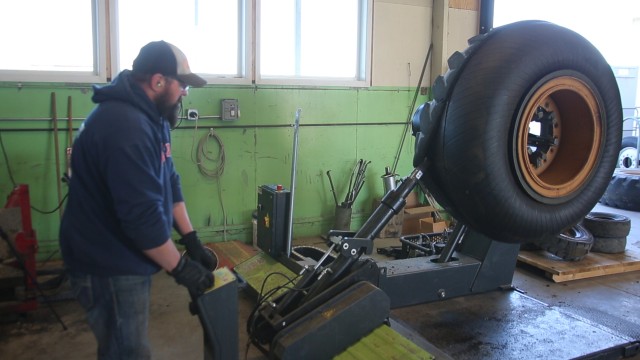
Sierra Army Depot equipment mechanics inadvertently created a hit YouTube video demonstrating their foam tire removal process tool. At last count, the popular video produced by the Sierra Army Depot Directorate of Information Management had garnered more than 7 million views on the social media platform.
The nearly twelve-minute long video shows the start to finish tire removal process with a wheel and tire placed on a modified tire mounting machine. A mechanic briefly explains the process and the tire machine starts slicing a large and well-worn tire that had seen use on one of the depot's many front loaders or heavy fork-lift vehicles.
The process, according to Ron Beauchman, a heavy mobile equipment mechanic supervisor for Sierra Army Depot in Herlong, California, was an innovative solution to the problem of removing foam filler from a worn out and useless tire. The foam filler, in turn, was a solution to a persistent problem of experiencing flat tires within the large heavy equipment fleet used to load, offload and otherwise move and transport everything sent in from the field and everything needing to be loaded up and sent back out.
Filling the tires with foam took addressed the flat tire issue, Beauchman said, and less vehicle down-time meant saving a lot of money for the Army and even some wear and tear on his mechanics.
The foam filler made a flat all but impossible, but it also greatly complicated removing a dead tire from an expensive wheel.
"We tried everything to remove the tires from the wheels, from using reciprocating saws to circular saws," Beauchman said, but the removal process was slow and exhausting.
"At the end of the day, my guys were just beat and their arms were jelly."
The slow process, he added, allowed for just a handful of tires to be dismounted per week.
About two years ago, the idea of modifying the tire machine was born. Beauchman figures that fabricating a couple of blades to the tire machine has saved the Army more than $1.2 million annually so far in tire costs, vehicle downtime and labor costs.
"Now the process takes anywhere from twelve minutes to about an hour to remove a tire," he said adding that the greatly improved process allows mechanics to keep their vehicles up and running at a much higher rate.
The YouTube views count and comments from around the world seem to indicate that the foam tire removal process is not only popular, but most likely preventing jelly arm around the planet.
"We're very pleased that Sierra Army Depot is getting recognition for something that is basically just looking out for our employees," Beauchman said.
# # #
About Tank-automotive and Armaments Command:
TACOM's six manufacturing arsenals and maintenance depots generate operational capability throughout Army formations as part of the Army's Organic Industrial Base. When the force needs equipment or parts manufactured, repaired, upgraded or modernized, industrial artisans from the Army's OIB deliver.
TACOM's workforce includes highly skilled and uniquely qualified professionals, from industrial artisans to senior logisticians and business analysts. The largely civilian workforce is critical to supporting Army readiness.
TACOM is responsible for the synchronization, integration and delivery of Soldier and ground systems materiel readiness solutions to ensure the Army is the world's most lethal and versatile fighting force.
Social Sharing