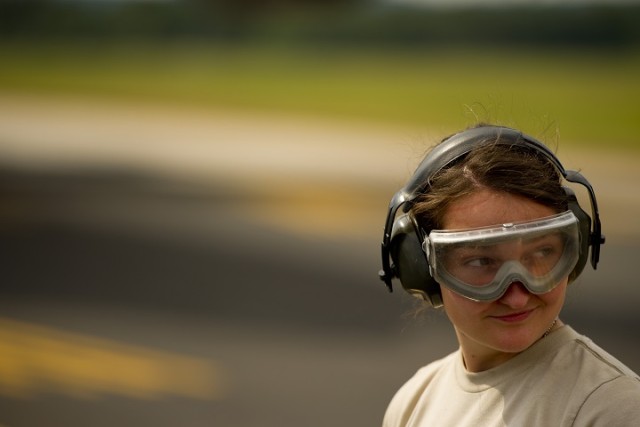
Industrial hygienists are scientists and engineers who study where you work and research the things you do every day, looking for ways you can do what you do safer.
Dr. Kirby Moss, chief industrial hygienist at Fort Knox, said that though it might seem an oversimplification, the industrial hygienist looks out for his fellow man.
"We simply survey the tasks that people perform [at Fort Knox], and we look to see what controls are available to eliminate hazards harmful to the worker," Moss said. "We monitor the work environment and we look for potentially harmful effects."
"We anticipate the worst that might happen, and we find ways to mitigate that."
Moss said industrial hygienists will investigate anything they suspect to be dangerous or anything employees are concerned about in the workplace, and that begins with a worksite analysis to determine which jobs and what part of those jobs have potential health detriments.
"We look at those things you do every day, and we investigate how [they] affect you now and how continued exposure will affect you as time goes on," Moss said. We identify harmful conditions and eliminate or mitigate them through [available] protective measures we find."
Derrick Lumzer, industrial hygienist with Ireland Army Health Clinic, said industrial hygiene is a mix of science and engineering.
"We are often confused with safety officers because just like they do, we put out information to keep [people] safe. Where we differ is how we're trained. We're trained to go a little further," Lumzer said. "It's a broad field, and we do everything from examine the work station and investigate [hazards] to using scientific methods to find out how dangerous [something is], to making a way to protect the worker from the danger."
Industrial hygienists protect the health and safety of workers in a myriad of ways, according to Lumzer.
"We'll do everything from investigate the ergonomics of your work station and the air quality of your office to looking for asbestos levels or levels of lead exposure," Lumzer said. "In your office or if you work in the elements, we are making recommendations to improve your work environment or developing some idea or technique to allow you to do your job without it costing you your health.
"You're working a job to support your family; we're working to support you so you can keep doing that."
Lumzer said one of his specialties as an industrial hygienist is hearing protection.
"One of the best ways and most immediate ways I help workers here at Knox is ensuring that workers are wearing ear protection," Lumzer said. "Hearing is one of the first things we begin to lose. It happens subtly, and people don't notice it from day to day. [Hearing protection] works if you wear it. I make sure they wear it."
Lumzer said hearing protection is probably how he made his greatest contribution to Fort Knox so far.
"Loud noises destroy your hearing, and so does constant noise, and sometimes people don't realize how quickly your ears [are] damaged," Lumzer said. "[The Recycling Center] had a real problem with their [brass] deformer machine. [Brass bullet casings] couldn't be [processed] here [because the noise level exceeded safe levels], and they had to send it away. Well, [that company] began charging Fort Knox to deform the brass, [only to] sell the [same] deformed brass for profit.
"Fort Knox wasn't making money from their brass; they were spending money so that others could make money."
Lumzer said that that loss of revenue was something Recycling Center Manager Daniel Sundeen thought could be turned around. Lumzer agreed.
"Sundeen asked if there was something that could be done for the existing deforming machine to get it into [compliance]," Lumzer said. "We collaborated together, and we looked and relooked at ways to overcome obstacles. We implemented possible solutions; trying to get the noise level to the acceptable level. No idea was stupid."
In the end, the solution turned out to be several solutions combined together.
"We needed a way to constrain the sound … and Sundeen had a damaged Cnex box that we recycled for that purpose … but that wasn't enough," said Lumzer. "We had to add special [sound absorbent] material that we insulated the Conex walls with. … We still had to use double hearing protection.
"We also had to ventilate the whole thing to mitigate higher than safe lead levels. That took an exhaust system that vented out of the work area."
Lumzer said he was able to test and modify the apparatus so that eventually it passed stringent worker safety standards.
"We had to assess and reassess. I knew it would pass because it passed all the tests we apply as industrial hygienists," Lumzer said. "Eventually, Public Health Command at Aberdeen [Proving Ground in Maryland] gave us their approval."
The new device became not only a savings to the Army installation but also a financial boon. Lumzer said their success has spread to other installations and is changing the industry.
"Other installations wanted to know how we did it," he said.
Moss said that the company that produced the deformer is also interested and using some of Lumzer's ideas.
"It really has updated the brass deformer business," Moss said. "[Lumzer] accepted the challenge, and he wouldn't let go. … Hearing is important to the worker -- whether they know it or not -- and that's why it is important to him."
Lumzer admitted that some employees may grumble about the added steps now, but they'll eventually come around.
"They can thank me later when they can still [converse] with their grandchildren."
--30--
Social Sharing