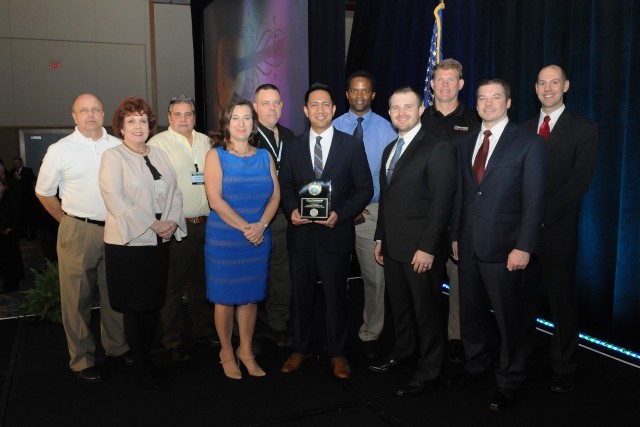
An Army project management team was presented with the Defense Manufacturing Achievement Award at the recent Defense Manufacturing Conference held in Tampa, Florida, in December 2017.
The award is based on significant improvements in manufacturing cost and time for the Army's newest 7.62 mm bullet.
The Project Manager Maneuver Ammunition Systems (PM MAS), part of the Program Executive Office Ammunition at Picatinny Arsenal, the U.S. Army Armament Research Development and Engineering Center (ARDEC), and the Army Research Laboratories developed the XM1158 7.62mm Advanced Armor Piercing Ammunition.
The XM1158 provides improved performance against a broad spectrum of battlefield barriers and targets typically engaged by dismounted infantry using small caliber ammunition, explained Stephen McFarlane, XM1158 program management lead.
The new bullet is replacing the legacy 7.62 mm armor piercing ammunition, the M993.
"In the last decade, many improvements have been made in small caliber ammunition resulting in the improved general propose round, the M80A1 7.62mm Enhance Performance Round (EPR). The XM1158 retains the improvements fielded in the M80A1 7.62mm EPR with the addition of enhanced hard-target effects resulting from its tungsten carbide penetrator," McFarlane said.
Tungsten Carbide, abbreviated as WC, is typically used in the penetrator of armor piercing bullets. However, producing WC components at high volumes presents manufacturing challenges.
"This in turn has required research in advanced manufacturing techniques," said McFarlane. "Without these advanced manufacturing processes, the cost of bullets and time to manufacture them would have increased significantly."
To mitigate significant cost and schedule impacts, the government invested in a three year Manufacturing Technology effort that resulted in drastically decreased costs and cycle times for the manufacture of the XM1158 WC penetrator.
The successful manufacturing effort enabled the Army to go from baseline processing time of 15 minutes per round, to approximately 25 seconds per round, and achieved significant cost savings.
The new manufacturing process can be used across the suite of small arms penetrators, for an expected substantial return on investment.
Social Sharing