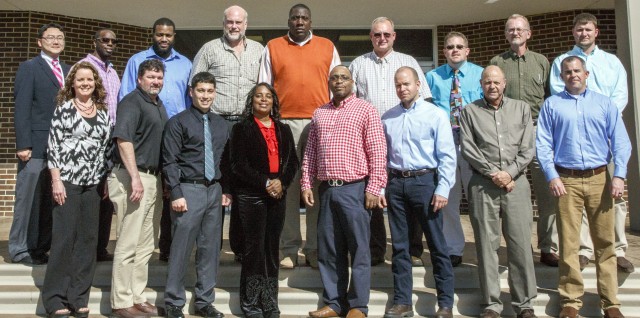
In 2009, Anniston Army Depot took control of the curriculum for its Depot Leadership and Management Program.
Prior to that time, the installation contracted with Jacksonville State University to train upcoming and current leadership throughout the installation.
With the current curriculum control, ANAD has been able to respond to requests presented from each class and implement changes in what has become a very fluid course.
"It's an ever-evolving curriculum," said Sean Perry, supervisor training instructor for the Training Office.
Each class follows a basic outline - with Civilian Education System courses, speakers from throughout the installation who share their leadership style and shadowing in various organizations.
Throughout the years as classes have asked for additional information on certain topics the curriculum has expanded to include Team Building and Situational Leadership courses from the Army Community Services.
Defense Acquisition University also assists the course with the Leadership 4-3-2-1 class, which is taught by a retired major general.
"We are allotted 300 hours from Defense Acquisition University, so we are utilizing that, especially with their location being so close," said Perry.
The course is aimed at employees who are GS or WG 11-12, but can accept, with command guidance, lower grade levels. This ensures those who are in supervisory roles, or may one day be there, receive first priority.
Earl Wood, a heavy mobile equipment repairer supervisor, had been in a supervisory role for years before taking the class in 2014. Immediately, he began to see ways he could improve the way he interacted with employees.
"Different people talk to the class and give different perspectives," he said. "One told us the supervisor sets the tone for his assembly line."
That comment struck a chord with Wood, who, during the course, spent time when his shop was on overtime to really look at the line.
"What you let happen becomes the standard," he said. "I noticed people were dragging around a little before getting started. I didn't want it to be that way."
For many employees who take the course, gaining an overview of how the depot operates and how things in one area affect other areas was informative.
"Everyone is each other's customer, right here on depot," said Doris Askew.
Askew was part of the first DLAMP class to complete the course entirely on the depot in 2009. She said the class really helped her be more customer-focused.
"When I go to the shops to work on shop instructions, they are my customer," she said. "It gave me more of a sense of pride in what I do and how I approach shop employees and listen to them."
"DLAMP is an eye-opener for a lot of employees. It gives them a better understanding of depot operations, since most spend their time in their own corner of the installation," said Perry.
Jonathan Lehr was a mechanic in the Directorate of Production when he took the course. Since that time, he has moved into the Directorate of Production Management and enjoyed learning about the various leadership styles, which he has found useful in his interactions with coworkers.
"If everyone who is working for you is happy, you aren't doing your job well because of the way individual work styles differ," he said.
Lehr wanted to see a speech portion added to the course, to enable class participants to learn skills for speaking in public.
While that hasn't been added yet, many other participant suggestions have.
The next DLAMP class, which will be held in the Fall, will be four weeks long, an addition of a week over the latest iteration of the course.
It is also scheduled to include more time with the Legal Office and the Civilian Personnel Advisory Center.
The distributed learning portion of the class has also changed.
"Instead of three sections with a comprehensive quiz at the end, it contains 10 sections with a quiz at the end of each section and a test at the end," said Bill Niemeier, an instructor for DLAMP.
Role-playing will also be incorporated into the next class as students have asked to be able to practice the skills they are learning.
The shadowing time with the various directorates will also change - moving from two days to two half days, each spent with a different leader from the installation who will be asked to provide an agenda for the time.
Perry credits the success of the class to its ability to change as the students' needs change.
"The command's willingness to allow flexibility and open dialogue make this course successful," he said.
The most recent class graduated DLAMP on Feb. 24. Employees interested in taking the course should speak with their supervisor.
Social Sharing