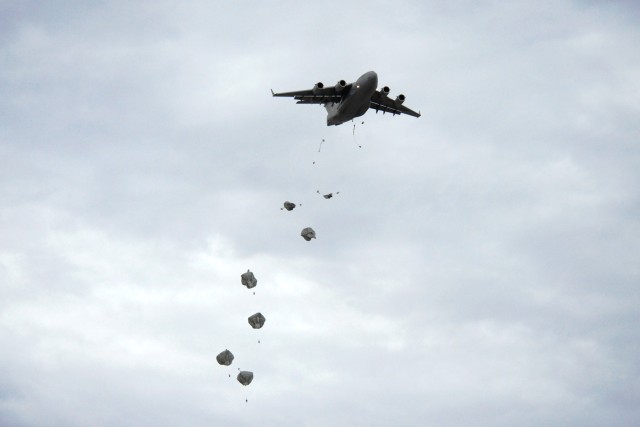
YUMA PROVING GROUND, Ariz.-- U.S. Army Yuma Proving Ground (YPG) is well known for testing virtually every piece of equipment in the ground combat arsenal.
The fruits of this testing include better and longer lasting equipment, as well as the ability to multiply a ground force more rapidly.
For example, prior to the first Gulf War in the early 1990's, the life-expectancy of the tracks used to propel an M1 Abrams Main Battle Tank along the ground was measured in the hundreds of miles. After extensive testing at U.S. Army Yuma Proving Ground, today's tank treads last for thousands of miles.
A more recent example of this high-impact, long-term testing is studies the proving ground's Air Combat Systems Test Directorate have conducted on the C-17 Globemaster to determine the heaviest weight the aircraft can safely carry. A follow-on study has looked at the amount of time and distance necessary between each element of a multi-element insertion of combat parachutists, known tactically as a mass exit insertion of the Global Response Force (GRF).
As air behaves like a fluid, the air disturbance left by massive cargo aircraft speeding through the sky is extremely turbulent and fast. The shedding of high and low pressures required for lift rolls up near the aircraft wing tips, resulting in powerful vortices that can remain over the drop zone for several minutes.
"It is very violent," said Keith Allen, team lead in the Aviation Systems and Electronic Test Division. "We're talking 150 to 200 feet per second in tangential velocity. It would definitely collapse a parachute if you got caught up in it."
The wings of military cargo planes are equipped with specially shaped finlets to help dissipate this vortex, but the extreme turbulence is still invisible and not able to be completely eliminated.. As a result, formations of C-17s carrying jumpers are required to keep a minimum distance from each other: if this distance could be safely shortened, more airborne Soldiers could reach the ground and enter a battle faster.
"The current spacing is based on a very conservative approach to ensure, in all conditions, that the vortices are dissipated or have moved off the drop zone in time for the next element of jumpers," said Allen. "The user community asked us to examine conditions where the distance between elements could be shortened."
In 2014, YPG testers undertook an ambitious two week study of the life cycle of these vortices, using a small Twin Otter aircraft equipped with Light Detection and Ranging (LIDAR), a surveying technology that measures reflections of particulates in the air by illuminating an area of regard with eye safe laser light. The Twin Otter was used to fly above a massive C-17, scanning the wake it left behind. The testers flew missions across all hours of the day and night, during different weather conditions and over different terrain features.
"Our intention was to go into the field to capture vortex data in operationally representative scenarios," said Allen. "We had to first understand the mechanics of the vortices and how they behaved in the field."
The LIDAR used to scan the air disturbances caused by the vortices is sensitive enough to pick up everything within the scanned area, including wind, thermals, and ground effects unrelated to the C-17 passing through the area. To be useful, this data had to be separated out from the effects of the C-17 in time and space, which was quite a challenge.
"We had to develop a mathematical algorithm that not only detected the vortex within all the rest of this noise, but separated it out," explained Allen. "That took several months: we then had to decide which factors about the vortex were most important."
Once the testers accomplished this feat, they compared the real-world data with predictions that had been made in computer simulations prior to testing. Going forward, YPG testers hope to conduct similar testing in different natural environments. Allen says the information learned in this testing is beneficial to other air drop activities, both at YPG and elsewhere.
"It gives YPG a lot of new capabilities as far as modeling, simulation as well as test methodology and new procedures for collecting wing tip vortices," said Allen. "The results of these studies are relevant to the entire aviation industry: there are LIDAR systems at large airports that look at the dissipation of vortices to govern their takeoff times for aircraft."
Data collection techniques developed for this study may have far reaching impacts on how wing tip vortices of both military and commercial aircraft may be studied in the future.
Social Sharing