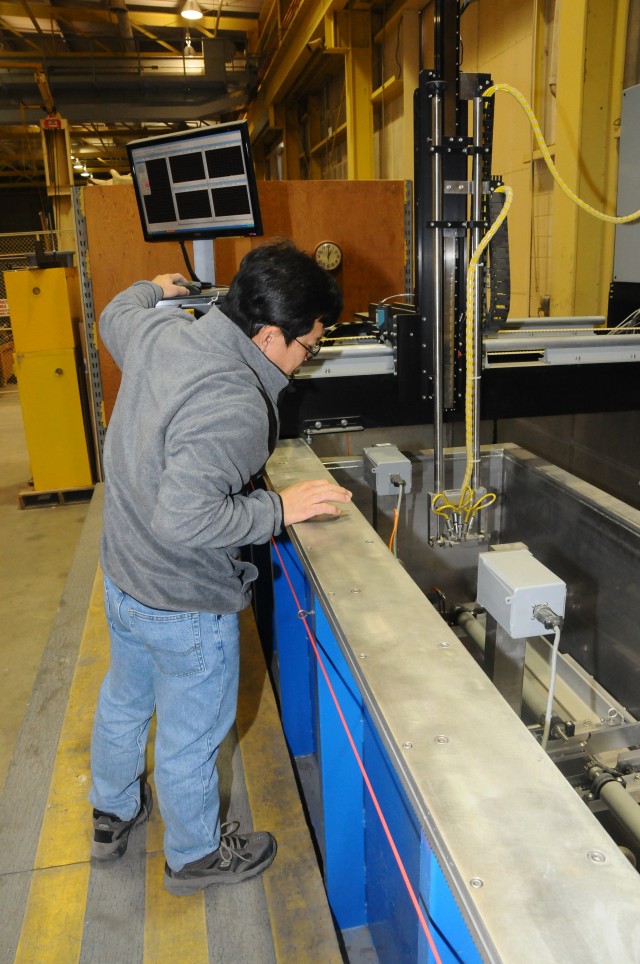
YUMA PROVING GROUND, Ariz.-- In an old proverb, a battle was lost because a horseshoe lacked a small nail that seemed insignificant.
In a modern day combat theater, a microscopic crack or bit of metal fatigue brought on by the tremendous, repetitive blast pressures artillery pieces are subjected to while firing could ultimately put a mortar or mighty howitzer out of commission, which could threaten Soldiers' lives.
At U.S. Army Yuma Proving Ground (YPG), non-destructive testing of everything from artillery to mortars to vehicle seats is an important, but sometimes overlooked part of the mission so far as the public is concerned.
In the test and evaluation world, however, YPG's Physical Test Facility is regarded as second-to-none, and David Le, mechanical engineer, and his team as among the most experienced professionals in the field. The recent ongoing efforts to add or upgrade equipment like an ultrasonic immersion equipment, a projectile imbalance measurement machine, laser bore mapping system, and portable measurement machines mean YPG's cutting edge advantage in this critical area remains razor sharp.
"Before, we had the ability to detect cracks 25 thousandths of an inch deep by 75 thousandths of an inch long," explained Le. "Now we have the requirement to look at finer cracks of five thousandths to 10 thousandths of an inch deep by 10 thousandths to 20 thousandths of an inch long, so the appearance is roughly as thick as a sheet of paper on the surface. We now have the equipment upgrade to define the smaller, higher crack on the bore surface."
The ultrasonic immersion machine was adapted for use for inspecting gun tubes from technology commonly used in the petroleum industry to inspect pipes. It uses water as the medium to impede the signal from a five channel transducer that electronically measures an object placed inside a massive tank. The outer tank holds 1400 gallons of water and can accommodate the tube or breach component of even the largest towed howitzer in the Army's inventory. A smaller, 300 gallon tank within the larger one can be used for smaller items like a mortar tube. The project planning to construct this began about five years ago, and will be placed into use in the near future.
"This new technology can be done here at YPG without the delay to ship an item to another laboratory or private industry to do it," said Le. "It makes a whole lot of sense for us to do it here all at once."
The transducer creates amazingly detailed electronic renderings of an item as is, but Le says it can be upgraded to have more data channels in the future, increasing the capabilities.
There have been other equipment upgrades in the lab, too. The proving ground's state-of-the-art laser bore mapping system, which previously had two data channels that rendered measurements accurate within one thousandth of an inch now has four data channels and is accurate to within one half of one thousandth of an inch. The lab also boasts a new portable coordinate measurement machine that is accurate to within two-tenths of one thousandth of an inch, a significant improvement over the previous one's seven-tenths of one thousandth of an inch accuracy.
"These can be taken out to the field to take the baseline inspection of high stress points in three dimensions," said Le.
However, when there is time to bring the item in question in for a comprehensive inspection, the lab's most accurate stationary machine can measure an object accurately within 50 millionths of one inch.
Non-destructive artillery testing also extends to projectiles. The proving ground has a projectile imbalance measurement machine that can detect the dynamic center of gravity and inertia of a shell. It operates on the principle of measuring balance in a tire, albeit in an inherently lethal artillery shell and uses a cylindrical device to hold the projectile firmly in place as it undergoes intense revolutions. This manner of testing is important as a projectile's propellant could shift inside, especially in extreme temperatures, thus making the projectile off balance.
"If it doesn't meet what the specification calls for, it could cause the projectile to fly incorrectly," said Le. "This is especially true with expensive guided rounds."
With all of these upgrades, the Physical Test Facility is well-equipped to continue Le's philosophy of test.
"A picture is worth a thousand words," said Le. "By the same token, one measurement is worth a thousand guesses."
Social Sharing