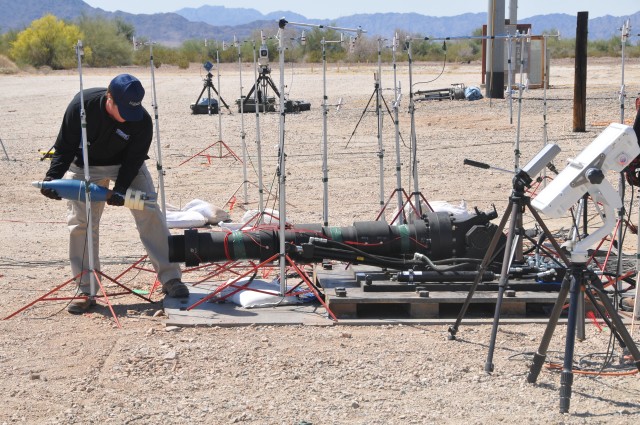
customers continue to choos... VIEW ORIGINAL
YUMA PROVING GROUND, AZ-- For versatility and power, the humble mortar has been a key indirect fire weapon for generations of infantrymen.
Quicker than calling in an artillery strike and capable of hitting targets at high angles, the mortar is likely to become even more important as technology makes mortar projectiles more accurate and maneuverable, and capable of reaching greater distances.
Though these advances have already led to mortar projectiles such as the GPS-guided XM-395 Precision Guided Mortar Munition, the mortar tubes from which they are fired have remained unchanged since the early 1990s. Currently, a ballistic tube for use with the 120 mm mortar, the largest in the Army's inventory, is undergoing initial testing at U.S. Army Yuma Proving Ground (YPG). Data from this cannon will support development of future mortars for warfighters.
"We are redesigning this tube because there have been developments within the 120 mm system in the propellant and projectiles that require the tube to do more than it really can," said Paul Koelbel, an engineer with the Army's Benet Laboratories. "Our goal is to design a new tube that will allow the existing and future 120 mm projectiles to do all they can do."
"Mortar cannon are in the field for 20 years," added Robert Cooley, design team leader. "What we put in the field five years from now has to be good 15 years from now."
One of the most important aspects of the early development is protecting Soldiers who use the tube in the future from harm caused by the tremendous concussion of a mortar round firing an arm's length away from their bodies. Though the tube has blast attenuators at the muzzle to direct the force away from the Soldiers firing it, the effects of a mortar report have been likened to the feel of 200 pounds of force hitting the body.
"The customer wants to create a pressure overblast profile that will help them determine where safe places for personnel firing the weapon are," said Ariel Melchor, test officer. "It will also determine how many rounds at different charges a user can take."
Toward this end, in addition to gathering the typical information about the characteristics of the mortar tube in action, the prototype cannon is surrounded by tripod-mounted sensors that measure overpressure in the areas around it.
"The goal behind everything we do is safety of the user," said Koelbel. "We need to have performance out of our equipment, but that performance can't come at the cost of the user. Our goal is to develop the safest and most resilient equipment so the user isn't in any danger from his own actions."
There are additional safety features for the team testing the prototypes, too. In addition to the standard practice of remotely firing all rounds, the weapons operators are protected by the prototype cannon's ability to remotely elevate and depress, a port to facilitate the extraction of misfired rounds using nitrogen, and the ability to be trigger-fired.
The performance characteristics of the tube and round are measured using the typical compliment of high speed cameras that can shoot thousands of frames per second, radar, and forward observers downrange.
"When we're able to bring a gun out to Yuma, the proving ground provides experienced mechanics and investigators," said Cooley. "When firing, we can rely on expert advice from people who maintain these systems on a recurring basis. From our scheduling standpoint, because of the weather and ranges available at Yuma Proving Ground, we can shoot at any range our cannons can reach, pretty much day in and day out."
"They are top notch people who really deliver the support and data we need," added Koelbel.
Social Sharing