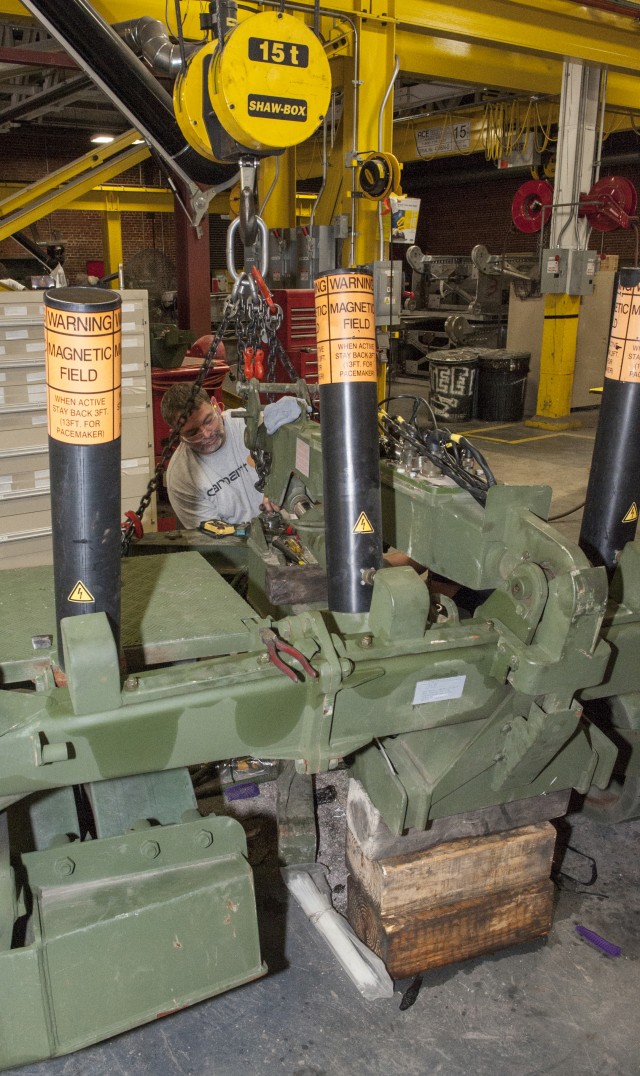
ANNISTON ARMY DEPOT, Ala. -- Aaron Glasgow had seen it numerous times. It was normal for the two-ton mine rollers to be placed on blocks of wood, sometimes wobbling a bit before settling into place.
"Every time employees took something off, the mine roller would shift," said Randy Houck, a mechanical engineer with the Directorate of Engineering and Quality.
Glasgow and his coworkers took precautions. They kept lifts attached to the equipment, holding the large pieces of metal in place.
But, there was a better way.
Through the safety suggestion program, the shop asked if a stand could be made to support the rollers while they are being disassembled or assembled.
"We need something more stable than we have now," said Glasgow, who made the suggestion. "Right now, we are using four wooden blocks - three at the front and one at the back of the mine roller."
Glasgow's entire shop has been tasked with looking at the processes employees perform every day to see if they can be done safer or easier.
"The goal is to find functional ways to improve their procedures," said Marcus Staples, supervisor for the Bridge Assembly and Repair Branch, which works on the mine rollers.
In response to Glasgow's suggestion, Houck established plans for a new support system for the mine roller. Once the plans are approved, they will be sent to the Directorate of Public Works which will fabricate the new support rack.
The fabrication process could take four to six months.
The stand will be constructed of steel and will use the basic concepts in place now for work on the mine rollers - supports in the front and back of the equipment.
However, these supports will hold the equipment more securely and include ways to tie the roller to the stand.
Rails along the bottom will allow the entire stand to be lifted and transported via forklift.
For Houck, creating stands such as this are a regular occurrence.
"This is one of the things we do every day," said Houck.
While fabricating a stand may be commonplace, replacing the electrical conduits for cranes in the largest building on depot isn't.
In 2012, the aging electrical lines along the Combat Vehicle Repair Facility's 14 crane runways were deteriorating.
"The old rails had a shoe which slid along the rail," said Quinton McRath, one of the crane operators. "As the electrical lines wore down, the crane would lose connection and cut off."
In places, the lines dipped, causing the crane to lose power.
When that happened, the crane's fail safe measures kicked in - the operator was no longer in control and the crane came to an immediate stop.
This sudden stop often caused loads carried by the cranes to swing, a dangerous situation in the crowded building.
McRath and other crane operators urged supervisors and the Safety Office to look into the issue and see what could be done.
The result was a new, enclosed track electrical system, which solved not only the issue of connectivity, but also eliminated the electrical contact hazard which had existed with the old system.
"There are now no metal parts where you can come in contact with the current," said Ken Lee, a mechanical engineer for DEQ.
Social Sharing