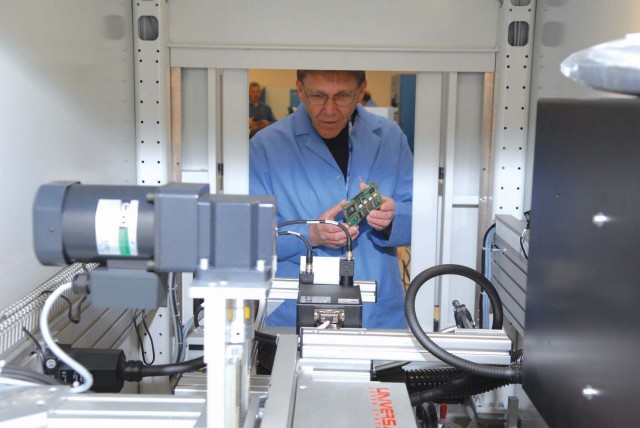
TOBYHANNA ARMY DEPOT, Pa. - Technicians are successfully remanufacturing a Data Transfer Device (DTD) system new to Tobyhanna.
"We began this remanufacturing mission in March 2008 with the arrival of the Technical Data Package and test equipment," said [Peckville resident] David Riley, chief of the Secure Telecommunications Branch, "The first device was remanufactured in June 2008 and we have a workload of 1,400 DTD's for FY08."
The branch is part of the Communications Systems Directorate's Communications Security (COMSEC) Division.
About 1,000 AN/CYZ-10 (V3) Data Transfer Devices, often called a Crazy 10 or DTD, have been remanufactured and tested for the Army's Communications Security Logistics Agency.
The device is used with the Single Channel Ground and Airborne Radio System as well as other controlled cryptographic equipment.
The AN/CYZ-10 (V3) is replacing the legacy family of Common Fill Devices, including the KYK-13, KYX-15 electronic storage devices, and the KOI-18 paper tape reader.
Technicians inspect, test and remanufacture the DTDs. Once a device passes the self-certification process, it is placed in storage until needed.
"We inspect the hardware and evaluate the software versions and this also involves two reloads of software applications," noted [Madison Township] Robert Malcolm, electronics technician.
COMSEC technicians practice Lean techniques, including Value Stream Analysis and Rapid Improvement Events, to "streamline the remanufacturing process," said [Weatherly resident] Phyllis Snyder, electronics worker.
"The point is that the technicians stepped up to the plate with their knowledge of Lean processes and their own Lean experiences," Riley said. "They understand the importance of the quality of these devices as well as the urgency of getting them back to the Warfighter in the field."
Robert Malcolm said they received help from personnel in the Production Engineering, Production Management and Public Works directorate's; the Productivity Improvement and Innovation (PII) Directorate's Quality Management Division; and COMSEC Division's Accountability and Documentation and Support Services branches.
"They helped to locate parts sources, set up the test equipment, and establish a procedure for the software applications, which is a very tedious process," said [Tobyhanna resident] John Peters, electronics technician. "The Quality personnel helped us establish an inspection point, final check and continuous improvement processes."
In Fiscal Year 2009, workload will increase to thousands of the devices. Riley said he is very confident the technicians can handle the larger mission.
"We've come a long way with the new mission workload," Riley said. "We only trained for this last year, and we're already seeing a significant increase from the preliminary numbers."
Tobyhanna Army Depot is the Defense Department's largest center for the repair, overhaul and fabrication of a wide variety of electronics systems and components, from tactical field radios to the ground terminals for the defense satellite communications network. Tobyhanna's missions support all branches of the Armed Forces.
About 5,900 personnel are employed at Tobyhanna, which is located in the Pocono Mountains of northeastern Pennsylvania.
Tobyhanna Army Depot is part of the U.S. Army CECOM Life Cycle Management Command. Headquartered at Fort Monmouth, N.J., the command's mission is to research, develop, acquire, field and sustain communications, command, control, computer, intelligence, electronic warfare and sensors capabilities for the Armed Forces.
Social Sharing