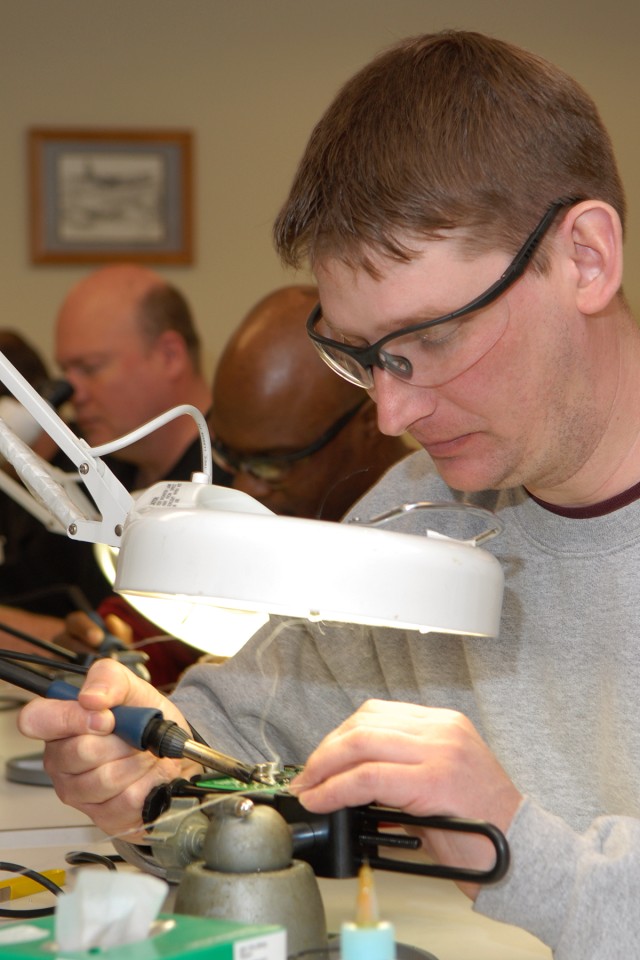
TOBYHANNA ARMY DEPOT, PA. - Tobyhanna now adheres to international standards for soldering in electronics circuits repair and cable manufacturing.
The Technical Development Division has two certified IPC trainers (CIT's), Mike Rosencranz and Bill Kimbell, to conduct training in four IPC soldering certifications. Certification means that all technicians will be using a set of approved industry standards, practices, instructions and techniques used by technicians throughout America and several other nations.
IPC, or Association Connecting Electronics Industries, is the organization that established standards for soldering that have been adopted by most major corporations worldwide.
American military organizations have adopted the standard as well, including the Army Materiel Command's Aviation and Missile Life Cycle Management Command and the Naval Surface Warfare Centers.
"IPC adopted standards based on best practices," said Bill Kimbell, a Technical Development Division training instructor. "Although we had soldering training here, it did not lead to industry recognized certification. Shops personnel began asking for a soldering certification to increase quality, improve yield and to attract more workload."
Kimbell noted that even technical schools do not offer comprehensive soldering training.
Four certifications give technicians knowledge in various subjects. Kimbell and Rosencranz characterize the classes as ranging from basic to expert. Technicians must be recertified every two years in each area.
IPC J-STD001 Requirements for Soldered Electrical and Electronic Assemblies. "This is the basic course for industrial-level soldering," Rosencranz said. "Our goal is to train all electronics technicians/mechanics for this certification."
This standard has emerged as the preeminent authority for electronics assembly manufacturing worldwide. The standard describes materials, methods and verification criteria for producing high-quality soldered interconnections.
It emphasizes process control and establishes industry consensus requirements for a broad range of electronic connections.
"This course is for personnel who do discrete wire to terminal, minor through-hole and surface mount work. It is also for quality inspectors and experienced electronics mechanics and technicians," Rosencranz said.
IPC 7711/7721B Rework/Modification and Repair of Electronics Assemblies. This course covers procedural requirements, tools, materials and methods for removing and replacing conformal coatings, surface mount and through-hole components. It also includes procedures for repairing and modifying circuit boards and assemblies.
Kimbell noted that this is the most difficult soldering course in industry aside from NASA specs.
IPC/WHMA-A-620 Requirements and Acceptance for Cable and Wire Harness Assemblies. "This certification is the most important process, materials and inspection standard for the cable and wire harness industry," Rosencranz said. "We'd like to see all cable shops personnel and associated inspectors certified in this training."
The training is lecture only and includes terminal soldering criteria.
IPC-A-610D Acceptability of Electronic Assemblies. First class is May 24. The most widely used inspection standard in the electronics industry, the course is targeted to inspector, leaders and self-certified shops. Kimbell noted that this standard is used by original equipment manufacturers and electronics manufacturing services companies worldwide.
This training is lecture only and available to engineers, inspectors, leaders, ISO-certified shops electronic technicians and experienced electronic mechanics.
"Technicians do not have to pass all modules to be certified, but all modules are taught. We offer remediation training and retesting in accordance with IPC policies and procedures," Rosencranz said. "All four classes include how to inspect work for quality using industry standards. About 200 technicians have taken the classes.
Tobyhanna Army Depot is the Defense Department's largest center for the repair, overhaul and fabrication of a wide variety of electronics systems and components, from tactical field radios to the ground terminals for the defense satellite communications network. Tobyhanna's missions support all branches of the Armed Forces.
About 5,600 personnel are employed at Tobyhanna, which is located in the Pocono Mountains of northeastern Pennsylvania.
Tobyhanna Army Depot is part of the U.S. Army CECOM Life Cycle Management Command. Headquartered at Fort Monmouth, N.J., the command's mission is to research, develop, acquire, field and sustain communications, command, control computer, intelligence, electronic warfare and sensors capabilities for the Armed Forces.
Social Sharing