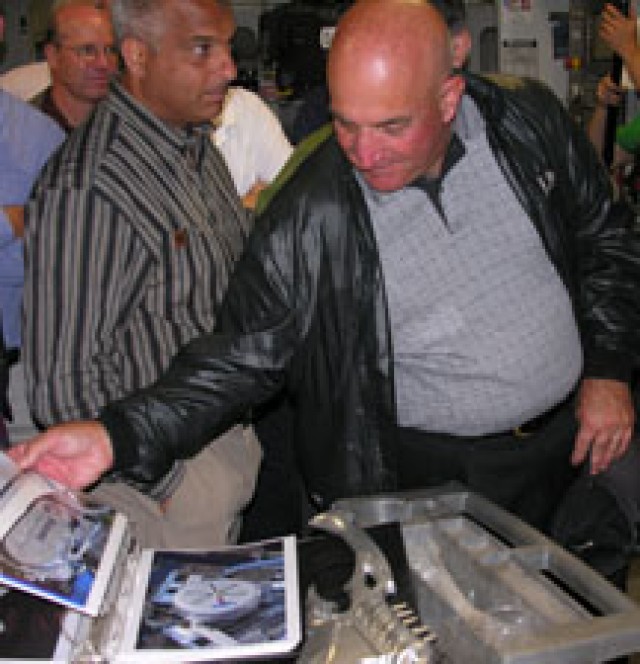
PICATINNY ARSENAL, N.J. - A group of approximately 15 Picatinny engineers and Soldiers visited the world-renown Orange County Choppers custom motorcycle manufacturing shop in Newburgh, N.Y., Aug. 28.
The purpose of the visit was for Picatinny engineers to tour the facility and discuss creativity, innovation and rapid prototyping capabilities as a benchmark for the Armament Research, Development and Engineering Center's innovation framework and process initiative.
Skip Creveling, president of Product Development Systems and Solutions Inc., said he coordinated the visit to OCC to "give ARDEC a unique perspective on the latest computer-aided conceptual design tools as well as rapid prototyping and fabrication methods."
For the past two years, PDSS has aided ARDEC to develop and deploy a state-of-the-art collaborative innovation framework.
Jim Quinn, lead engineer for OCC, led the tour and fielded all questions thrown at him while discussing how the company went from a small bike shop 10 years ago to one of the world's most profitable and notorious brands in the world through innovative design and custom parts manufacturing.
Quinn and Lt. Col. Brian Bosworth, director of the Munitions Engineering and Technology Center here, discussed prototyping issues that the Army has faced through the years, for instance, not being able to duplicate a proposed drawing or having to manufacture an older part when no drawing plans can be found.
"Our engineers will sometimes draw things that are entirely impossible," Quinn said.
Bosworth jokingly said, "Sometimes we have that same issue."
The comparison between OCC's manufacturing and the Army's is quite similar in that the customer provides the requirement and then has a very integral part of the development process.
"They listen and understand voice of customer. They get the customer involved from the beginning of the design concept until the product is completed," said Long Nguyen, a master black belt in the Lean Six Sigma Competency Office of the Quality Engineering and System Assurance Directorate of ARDEC.
The Soldier is the Army's customer and Army engineers develop weapons systems based on Soldier-need in the field. They also collaborate with service members during the entire design and development process to ensure the weapon will function as intended in theater.
One of the key talking points was the turnaround time that both OCC and ARDEC are required to uphold.
"ARDEC does a great deal of rapid innovation for the sake of our warfighters in Afghanistan and Iraq. They have to conceive, develop and field new counter-terrorism technologies in less than 90 days. The OCC paradigm of building one-of-a-kind bikes in three weeks was a good fit," said Creveling.
Social Sharing