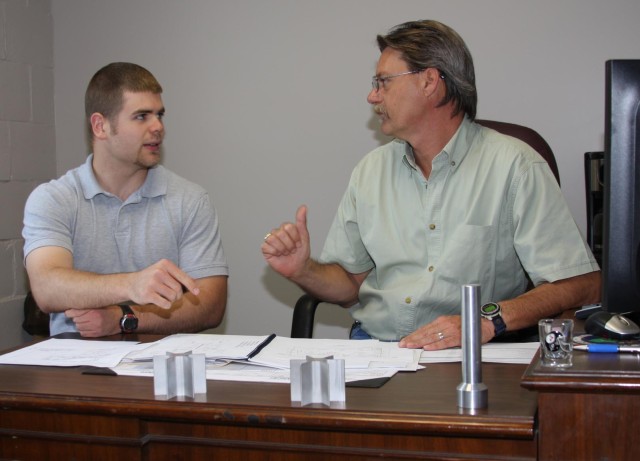
BLUE GRASS ARMY DEPOT, Richmond, Ky. - Three Eastern Kentucky University students recently worked with Blue Grass Army Depot personnel to research ways in which to improve the manufacturing process of the Depot's new 81millimeter mortar cartridge fin assembly project.
The Depot has been tasked with producing one of three types of mortar fin assemblies for the Department of the Army. The fin consists of two main components machined from aluminum and then coated and assembled into one complete fin. The project is a first-time endeavor at BGAD into the world of non-energetic (non-explosive) ammunition components. A core group of government, university and local industry subject matter experts collaborated on the project.
Through a bi-lateral agreement between the Depot's Directorate of Mission Operations Industrial Services Division and EKU's Industrial Technology Department, EKU senior project team members John Ryan, Samuel Arnold and Jeremy Hiler participated in the project.
"The Department of Army and our servicemembers will benefit tremendously from the efforts of these students. The knowledge and skills they bring to the table will help us become more efficient and effective in this production endeavor. We hope this partnering effort will lead to additional opportunities for EKU students at the Depot, "says Depot Commander Col. Joseph Tirone.
EKU Industrial Technology Department Professor Ted Lloyd says, "The students benefit from getting to put into practice four and a half to five years of classroom theory. The students get to work with very knowledgeable people who provide excellent critical feedback about their progress. The opportunity allows EKU to showcase its talent base and helps create a working relationship with companies."
"I always like working with companies who are willing to help students learn. The projects are a win win for all involved," Lloyd adds.
The student team collected and analyzed data to determine opportunities within the project scope for improvement in areas such as cost, schedule, quality, safety, cycle time, efficiency, ergonomics and environment. They documented their findings and the process for evaluation in determining recommended improvements. The team provided periodic updates on their progress and then compiled a final report of findings and recommendations to BGAD management.
The areas researched were simulating the process flow (how the product is going to be produced and why the process flows the way it does) using software; recommending options for quality check/assurance methods that can be used during production and proposing construction production layouts oriented around lean manufacturing concepts.
The student team selected and used a simulation software designed for evaluating, planning/designing manufacturing, warehousing, logistics and other operational and strategic situations. It allowed the team to change almost any aspect of the manufacturing process without physically doing it and allowed them to see mistakes and problems prior to these actually occurring.
"The software's flexibility and versatility are critical to the Depot's mortar fin assembly project because the process requires customized equipment to be developed and tested in order to successfully assemble the mortar fin parts," says Timothy Delozier, the Depot's 81mm mortar cartridge fin assembly project officer.
During this phase of the project, the team found the software not only benefitted this project but could also be used for many other Depot projects and processes.
"This software application also could be used in the Depot's current ammunition maintenance projects and ammunition receiving and shipping operations," Delozier says.
The student team was also tasked to recommend options for quality check/assurance methods that can be used during production. This is especially important with this project because the 81mm mortar fin must be within specific tolerances and, for maximum quality assurance, each part needs to be inspected after each machining process.
Arnold, who helped the other two team members with quality assurance, notes its importance with this project.
"The whole goal is "lean" manufacturing which reduces ergonomic issues, increases productivity and efficiency and reduces the cost per unit," explains Arnold.
During this phase of the project, the team conducted research on all the machines being used in the mortar fin project. The team proposed optional production plan layouts to best incorporate automation and locations for the quality assurance stations.
Recommendations were made to incorporate automated gauging techniques to increase productivity and quality assurance. The team also found that while automated quality checks would benefit this project, manual gauging would still need to be available.
The final area of consideration was researching and proposing several different layout designs with increasing levels of automation with cost analysis associated with each.
The four-month project was coordinated through the Depot's Lean Six Sigma Division whose personnel monitored the project.
Depot personnel indicated the student project team's efforts are being incorporated into the project.
"We've already adapted some of their ideas and have applied these in producing custom machinery for our July first article testing run," says Delozier.
###
Social Sharing