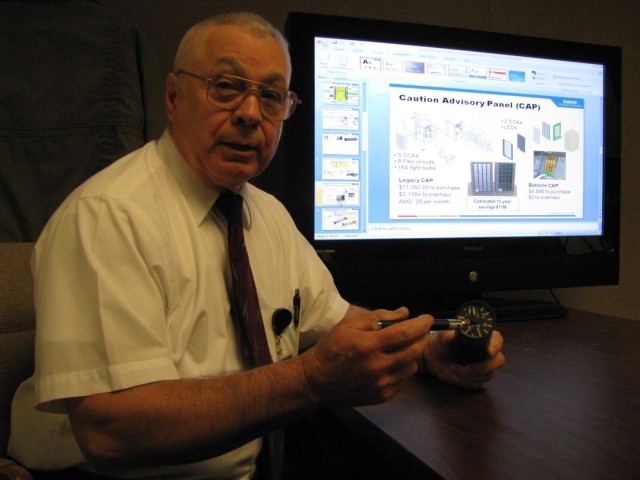
There's a government-industry partnership team at Redstone Arsenal that is catching the attention of aviation and missile system leaders throughout the Army and Defense Department.
The partnership - designed to update existing and aging weapon systems while also cutting costs, speeding up the design, production and acquisition processes, and providing the best equipment possible to the war fighter - is known as Continuous Technology Refreshment. It is a DoD-wide program that has been implemented successfully by the Integrated Materiel Management Center for the Aviation and Missile Command.
"CTR is a life cycle management success story for AMCOM," said Alan Miller, chief of maintenance information operations for IMMC. "AMCOM is a model of how to make CTR work. This is a high priority program to (AMCOM commander) Maj. Gen. (Jim) Myles and IMMC director Eric Edwards."
CTR allows the command to work closely with industry to address sustainment issues in regard to the safety and readiness of aviation and missile systems. Sustainment issues can involve decreased reliability, high cost and diminishing manufacturing sources.
"The intent of this program from the beginning has been to modernize our equipment by doing one spare at a time to improve performance and reliability, increase Soldier readiness, reduce maintenance time and lower costs," Miller said.
"We wanted to modernize spares without using government research and development money because R&D money is limited and there's a very competitive R&D process. R&D money often also doesn't cover all the requirements. In addition, guidelines wouldn't allow us to use spares production money to do a re-design, and a DoD acquisition process for a newly designed spare is lengthy. So, it was decided we needed an acquisition strategy that didn't follow the DoD acquisition process."
The standard acquisition process for military hardware involves detailing requirements, defining a program and budgeting funds.
"That can take several years to materialize or be successful," Miller said. "It is the Office of the Secretary of Defense belief that technology would change or evolve several times before that process could be complete. So we needed a way to get outside the DoD process. CTR became DoD's way around the acquisition process."
In early 2002, AMCOM took steps to enter into a partnership with industry that suggested industry would fund the CTR process.
"CTR is about the re-engineering of a part to arrive at a production solution," Miller said. "The re-engineering is done by industry at their cost, and then the part is produced under the normal production process for spares. The industry that does the re-engineering teams with a production company and recoups their costs."
Two companies - Battele of Columbus, Ohio, with offices in Huntsville and Sparta of Huntsville -- are teamed with AMCOM to re-engineer spare parts while two other companies are AMCOM's production partners for those parts. Electronic parts are produced by Alaskan-native owned Tyonek, which has a facility in Madison, and mechanical parts are produced by a small disadvantaged business known as Adept of Huntsville.
One example of a redesigned spare is the caution advisory panel on the Black Hawk helicopter.
"The old CAPs required 164 light bulbs that were always burning out. Pilots were known for carrying pockets full of light bulbs. It also had five circuit cards and eight flex circuits that all had to be maintained," Miller said. "The new CAP has only two circuit cards and all LED lights. The change reduced cost, cut down on maintenance and created a weight reduction."
Other examples include the cryogenic coolers on the Avenger and TOW-II missile systems, which were made more reliable, lighter in weight and less expensive to maintain.
"In every case, the spare is redesigned and qualified. It is produced and fielded, and we own the new design specifications," Miller said.
Redesigns have one rule to follow - the rule of form, fit and mission function.
"The interfaces with the overall system have to be the same. The new hardware has to be able to fit in the same place as the old hardware. And the signal strengths have to be the same," Miller said. "The aircraft or missile system can't know there is a difference."
Spares are earmarked as possible candidates for CTR by item managers when cost, reliability, readiness or production sources become an issue. Miller works with industry to do a Business Case Analysis based on a spare part's age, design, quantity and use, and then builds a contract requirements package to put the spare on a production contract. Throughout the CTR process, Miller works closely with industry partners as well as the program executive offices and program managers for aviation and missile systems.
"In a normal acquisition process, it can take 10 years to justify re-engineering. We can take that same part and re-engineer and qualify it, produce it and put it in the field in two years," he said. "Spares that go through CTR meet all performance requirements and are granted Air Worthiness Release."
CTR maximizes Soldier readiness by providing higher reliability at lower costs.
"The commanders in the field have a limited budget to work off of," Miller said. "When their systems are stressed because of reliability, they can't always buy everything they need to maximize readiness. CTR helps their budget situation by fixing low reliability parts at much lower costs. In every case, we've seen at least a 50 percent reduction in costs. CTR allows them to use their money on other things, resulting in a more efficient use of money."
When the CAP was redesigned, the cost per unit went from $11,392 to $4,886 and overhaul costs went from $2,176 per unit to zero per unit. Estimated cost savings over 10 years are $18 million. Savings for the Avenger and TOW cryogenic coolers, respectively, are estimated at $7 million and $18 million over 10 years.
Another spare that is undergoing redesign is the Black Hawk navigation system, which will be more reliable and will save $375 million over 10 years.
In all, the program's current 32 redesigned spares - which are now either fielded, under contract for production or in the business case analysis stage in preparation for production - will save $869 million over 10 years.
"CTR is a DoD mandate. It is a sustainment strategy that will continuously refresh the technology of aviation and missile systems," Miller said. "But, most importantly, it is a program that will modernize spares, improve reliability, increase readiness and improve performance for Soldiers on the battlefield."
Social Sharing