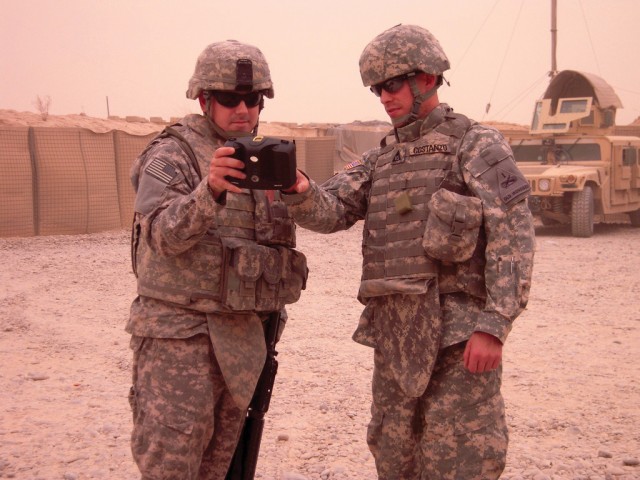
TOBYHANNA ARMY DEPOT, Pa. - Tobyhanna's ability to make on-site repairs to communications-electronics equipment extends the scope of its maintenance and logistics mission from the mountains of Pennsylvania to the deserts of Southwest Asia.
Hundreds of depot employees deploy each year to more than 20 Forward Repair Activity facilities to support expeditionary logistics missions in Iraq, Kuwait and Afghanistan. Military members from all branches of service depend on Tobyhanna's skilled technicians to fix systems and components damaged in the hostile environment.
"We have the capability to move a very flexible, adaptable, and responsive workforce where it needs to be when it needs to be there," Depot Commander Col. Ron Alberto said, pointing out that a large percentage of the depot's workforce works outside the installation. Tobyhanna has a worldwide net of more than 65 FRAs.
Tobyhanna volunteers support various repair missions: Firefinder radars, Warlock electronic countermeasures, communications security systems, and command, control and computers. The depot also provides embedded support to the Army's intelligence system, Guardrail. These warzone initiatives are directed by officials in three directorates with deployment lengths averaging six months.
It seems Tobyhanna has found a way to build an FRA around any mission, according to John Parada, C3/Avionics Directorate's FRA Division support program manager. "We have the skills here to run the gamut allowing us to send teams anywhere to do anything," he said.
The repair activity's main objective is to provide a quick turnaround on repairs while eliminating costly shipping charges, according to James Kondratick, COMSEC FRA project officer. To date, sites have received and processed 18,546 in-field repairs or direct exchanges.
"We have outstanding individuals representing the depot and supporting the men and women engaging the terrorists threatening our way of life," said Kondratick. "Whatever it takes, we do it."
He explained that technicians repair, test and modify secure communications equipment in customized shop vans. They also provide direct exchange services for equipment that cannot be repaired in a reasonable amount of time. The vans that support all FRAs are shipped from Tobyhanna fully loaded with tools, test equipment and parts.
"We often see Soldiers covered in sand with an M-16 slung over one shoulder," said Chuck Bartleson, electronics mechanic, adding that his sense of accomplishment from working on one item for a waiting warfighter is equal to working on 100 components at the depot. Bartleson speaks from experience, having deployed twice for a total of 14 months.
A month-long training course prepares COMSEC volunteers for deployment. The course covers mission, security, accountability, and shipping information. Individuals must also complete a certification course which enables them to repair COMSEC equipment.
Randy Nielson is participating in his third deployment supporting the COMSEC mission. "You'll never do anything more personally rewarding, but think long and hard, and consider the sacrifices involved," he said, explaining that even though he has missed birthdays and anniversaries, his wife continues to back him 100 percent. Nielson is a team leader in Iraq.
Tobyhanna's Firefinder Systems Division supports repair activities in Iraq and Afghanistan. Technicians support the AN/TPQ-36 and AN/TPQ-37 systems, component level work, and the AN/TPQ-48 Light Weight Counter Mortar Radar.
"Our FRA teams demonstrate a high-level of technical competence providing system readiness to our warfighters 24 hours a day, seven days a week," said Daniel Shea, Firefinder Systems Division chief, adding that operations are very flexible and extremely versatile.
"Expect to work long hours," said John Morelli, digital computer mechanic. "But be prepared to gain a lot of personal satisfaction in completing a job well done." Morelli repairs Standard Army Management Information Systems equipment such as computers and printers.
Tobyhanna employees tackle environmental hazards such as sand, heat and moisture on a daily basis while repairing and testing complex electronic systems and components. And, despite the long hours and austere conditions, everyone agrees there's no job more rewarding than helping America's service members.
"This job is very gratifying," said Scott Beck, supply technician. "The Soldiers need us and we provide a valuable service that makes their difficult job a little easier."
Beck orchestrates FRA activities for COMSEC operations around the globe. From his desk at the depot, he is able to replenish supplies, fill positions and file reports based on information gathered from the field.
"I know our customers appreciate what we do," Nielson said. "They tell us all the time." As team leader, he oversees the day-to-day operation of the shop such as recording transactions, maintaining records, ordering supplies, and managing all shipping and receiving. Nielson noted that it would take weeks or months for Soldiers to get their equipment repaired or replaced without Tobyhanna FRAs. "With us here, turnaround time is 24 hours or less."
The depot's largest FRA operation directs requirements for several C3 programs such as Command Post System & Integration (CPS&I), Air Defense and Airspace Management, Counter Rocket Artillery Mortar, Common Ground Station, and Handheld Interagency Identity Detection Equipment.
"This program just keeps growing," Parada said. "It's a highly diverse mission and computer repair is only about one-third of the workload." Support for the warfighters and quicker turn-around is precisely why the depot continues to expand the FRA program," he added.
An asset of the FRAs specializing in computer repair is that the technicians are certified to work on many of the computer systems that the military uses. In most circumstances, equipment is repaired and returned in less than 24 hours.
"FRAs provide immediate support to the warfighter's mission critical equipment and training efforts," said James Ashton, a process improvement specialist embedded with an Army division in Iraq. Ashton travels throughout the country supporting Soldiers in the area of operation where his responsibilities include training troops on the effectiveness of biometrics and HIIDE system user operations.
"I would recommend deployment to anyone seeking personal and job-related satisfaction," he said. "Our mission is appreciated by all levels and branches of the military."
"FRAs are manned by the boldest, brightest and best Tobyhanna has to offer," Kondratick concluded.
Tobyhanna Army Depot is the largest full-service Command, Control, Communications, Computers, Intelligence, Surveillance, and Reconnaissance (C4ISR) maintenance and logistics support facility in the Department of Defense. Employees repair, overhaul and fabricate electronics systems and components, from tactical field radios to the ground terminals for the defense satellite communications network.
Tobyhanna's missions support all branches of the Armed Forces. The depot is the Army Center of Industrial and Technical Excellence for Communications-Electronics, Avionics, and Missile Guidance and Control Systems and the Air Force Technology Repair Center for ground communications and electronics.
About 5,700 personnel are employed at Tobyhanna, which is located in the Pocono Mountains of northeastern Pennsylvania.
Tobyhanna Army Depot is part of the U.S. Army CECOM Life Cycle Management Command. Headquartered at Fort Monmouth, N.J., the command's mission is to research, develop, acquire, field and sustain communications, command, control, computer, intelligence, electronic warfare and sensors capabilities for the Armed Forces.
Social Sharing