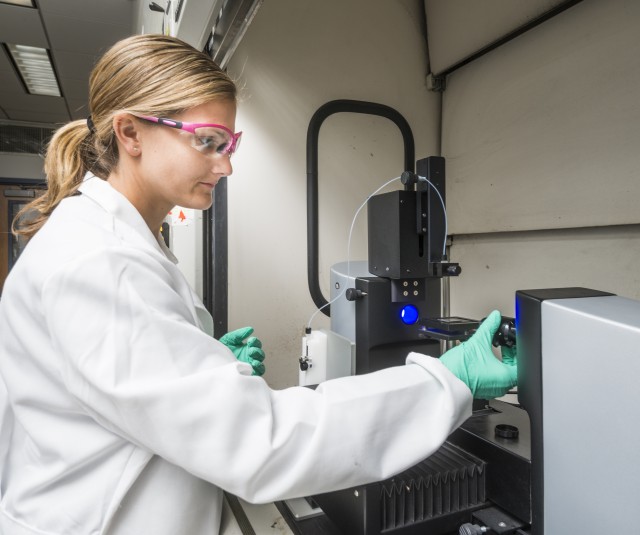
NATICK, Mass. (Sept. 29, 2015) -- For Molly Clay, great science comes in small drops.
Clay works on the Integrated Protective Fabrics System project and is a research chemical engineer on the Chemical Technology Team at the Natick Soldier Research, Development and Engineering Center, or NSRDEC. Researchers on the team measure chemical agents entering barrier materials, such as clothing, by using different experimental techniques. Clay is working on a new approach that involves tracking a minuscule drop of liquid placed on the surface. The method is convenient and well-suited for working with toxic materials in the laboratory.
"We have all these new protective barrier materials that can be applied to uniforms, boots, gloves, face masks -- anything you use to protect yourself," said Clay. "We needed a way to characterize these materials. We wanted a way to measure how liquid chemical agents go through the materials to see if these materials have the qualities we want."
"NSRDEC researchers look to innovate in many ways," said NSRDEC's Dr. Ramanathan Nagarajan, Senior Research Scientist Soldier Nanomaterials. "Molly's work is an example where the experimental technique has been known in the literature and is not new. However, the technique is not used as a routine test method because the data analysis requires time-consuming and costly numerical computations.
"Molly's innovation is in the creation of a simple analytical model, which totally eliminates the computational complexity and is also very accurate. This innovation in modeling will allow us to use this drop-image technique as a standard test method to evaluate how well any barrier material prevents the entry of a liquid chemical agent."
Sometimes in the past, immersion methods were used and relied upon large quantities of liquid. Clay explained that measuring changes in large quantities can prove difficult at times, and she has instead has opted to work with very small quantities, using only one to two microliters.
"We first look at the droplet on an impermeable surface, like stainless steel or aluminum, because you know liquid is not going to diffuse into the surface," said Clay. "Any changes in volume are due to evaporation going into the air -- so we first account for any evaporation. I then monitor a droplet on a permeable substrate. I can take any evaporation into account and only look at what is going into the substrate. This is going to give me a diffusion coefficient and show how fast something is going to diffuse into the barrier material. And from that you can determine the level of protection."
Using only a drop is a safer, more cost-effective and more efficient way to test the level of protection than using larger quantities of liquid. To measure contact angles, Clay uses a goniometer, which is an automated instrument that monitors continuously the drop shape on the surface.
"We're taking that one to two microliter droplet, and we are placing it on the surface," Clay said. "I'm monitoring it over time and measuring the contact angle of the liquid with the surface. And through the geometry of the shape of the droplet, you are able to determine the volume. So, now we have volume versus time on a specific surface. From there I developed a model that will determine the diffusion coefficient."
That information is then used to improve products for the warfighter.
"We can use the information to determine the most effective existing materials or to aid in the development of novel materials," said Clay.
A little drop of science can have a huge effect.
"My work is at the basic research level, including developing new tests that will help enable us to make better decisions regarding products for the Soldier," said Clay. "To have that kind of impact, to be doing something that is going to benefit the Soldier down the road, is the best part of the job."
-------
The U.S. Army Natick Soldier Research, Development and Engineering Center is part of the U.S. Army Research, Development and Engineering Command, which has the mission to ensure decisive overmatch for unified land operations to empower the Army, the joint warfighter and our nation. RDECOM is a major subordinate command of the U.S. Army Materiel Command.
Related Links:
U.S. Army Natick Soldier Research, Development and Engineering Center
Army.mil: Science and Technology News
Social Sharing