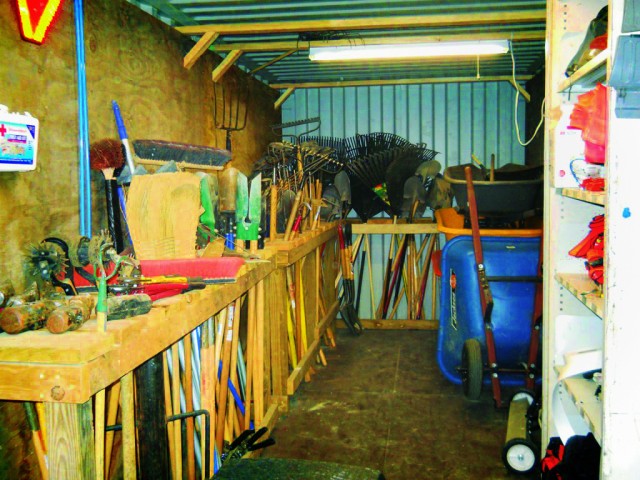
The 5S workplace organization method is the foundation of the lean manufacturing strategy that emphasizes eliminating waste while delivering quality products with greater efficiency. This article details how applying the 5S system (sort, set in order, shine, standardize, and sustain) transformed supply and warehousing functions at Camp Mackall, N.C., a training facility for the John F. Kennedy Special Warfare Center and School (SWCS) at Fort Bragg, N.C. The article discusses the terminology, methodology, and practical application of 5S.
FREEDOM TRAINING FACILITY
The SWCS manages and resources professional growth for Soldiers in the Army's three special operations branches: Special Operations Forces, civil affairs, and military information support. The 3rd Battalion, 1st Special Warfare Training Group (Airborne), is the home of civil affairs training for the SWCS and the Army. The battalion's C Company is responsible for field skills training and provides logistics support to other 3rd Battalion companies for field training.
The company is responsible for maintaining and expanding the battalion training facilities. The Freedom Training Facility at Camp Mackall is the battalion's primary location for field training. The facility has an urban reaction facility, a forward operating base, patrolling areas, and a village that simulates conditions in economically developing nations. About 3,000 Soldiers train annually at the facility.
In 2011, the Army began expanding its Reserve component civil affairs structure by adding a brigade to meet the expected increased demand for civil affairs support by 2013. In 2010, the Army Reserve began adding a brigade to bring its civil affairs companies from 112 to 132 by 2012. The increased training requirements for C Company required the expansion of the Freedom Training Facility.1
The village at the training facility became the temporary site of the C Company headquarters. The village sat on nearly 12 acres of pine forest and had 12 buildings and some smaller structures. Plans called for as many as 20 buildings, sleeping areas for 80 role players, and a facility management operations area.
Before C Company, which was formally established in April 2011, took over the training facility, one person managed it for five years with an annual budget of only $80,000--barely enough to cover the facility's maintenance. Since C Company took over, the battalion has spent nearly $5 million in upgrades and completed more than $900,000 worth of troop labor projects.
LEAN MANUFACTURING
The concept of lean manufacturing was made popular in the 1980s by the Toyota Motor Corporation but has its roots in automotive production as early as 1910 with Henry Ford's manufacturing system used to produce the Model T. Corporate executives worldwide were exposed to the concept in 1990 with the publication of The Machine That Changed the World by James P. Womack, Daniel T. Jones, and Daniel Roos. The book details Toyota's lean production system that serves as the basis for its success.
Lean production focuses on driving waste out of the work cycle. Lean practitioners seek ways to accomplish more with less time, space, equipment, people, and resources.2
According to the Lean Enterprise Institute, "the core idea is to maximize customer value while minimizing waste. Simply, lean means creating more value for customers with fewer resources. Eliminating waste along entire value streams, instead of at isolated points, creates processes that need less human effort, less space, less capital, and less time to make products and services with far less costs and with much fewer defects, compared with traditional business systems."3
Lean is a way of thinking. The tools specific to manufacturing may not all apply directly to service industries; however, some translate fluently. One of the most powerful Lean manufacturing tools, and a cornerstone of any successful implementation, is 5S, which stands for the Japanese words seiri, seiton, seiso, seiketsu, and shitsuke. The English translations are sort, set in order, shine, standardize, and sustain.
5S is a simple tool for organizing a workplace in a clean, efficient, and safe manner in order to enhance productivity and ensure the introduction of standardized processes.4 Each step decreases waste and increases the ability of the operator to complete a task to the standard or quality the customer desires.
SORT. This step removes all items not necessary for the current operations. Some companies conduct "red tagging." This process identifies questionable items and places a red tag on them. If the tagged item is not used after a few days or weeks then it is deemed not essential.
SET IN ORDER. This step organizes a work area for maximum efficiency. Organization and orderliness work best when implemented together. Set in order means arranging items so that they are easily accessible and labeled. Labeling is mostly for others who need to know what is in the area when the area owner is away.
SHINE. This step is what most people think of when they hear 5S mentioned. This is the step in which operators clean the workstations. Cleaning the workstation not only removes defects but also leaves the site ready for work at any time.
STANDARDIZE. All procedures should be consistent and standardized so that employees complete specific functions in the same manner. Workstations for like functions should be identical. Since everyone has a different perspective on what is clean, standards for cleaning are created during this step.
SUSTAIN. This step requires self-management and auditing from inside and outside the organization. The idea is to maintain the progress and continue to evaluate the process for waste. Many companies regularly audit their processes to ensure the employees are still adhering to 5S principles.
TRAINING FACILITY PROBLEMS
The problems facing the training facility and its management included a lack of established systems for storage, nonstandard repairs, the overuse of the site for storage, and an abundance of stock materiel.
Before implementing 5S, all supplies were delivered to the facility manager's office. Large amounts of materiel were unloaded into several cleared areas used as lay down yards--areas to stage equipment and supplies for future projects. Smaller or expensive items were unloaded into one of eight shipping containers. However, items were placed randomly into the containers. Often, completing a single project involved looking through all eight containers to find the necessary materiel.
Also, materiel was purchased in bulk or recycled from previous building projects. Materiel and tools were often moved several times because of the inability to store those items at the building site. This caused redundant efforts, damage, and loss of accountability.
At one time, nearly $500,000 worth of construction materiel was on the ground and in the containers. Only about $200,000 worth of the materiel was slated for projects within the next six months. About $300,000 worth of goods were simply in the way, rotting, rusting, or generally losing value and costing money and effort to store.
Standardized procedures had not been established for facility maintenance. Many of the Soldiers had no construction training and learned on the job. Soldiers did their best to make necessary repairs, but this approach meant that repairs were not standardized.
TRANSFORMING THE FACILITY
Applying 5S to the facility and its operations started with a planning phase followed by an execution phase.
SORT. The plan was to remove all materiel from the shipping containers and the lay down yard. Unneeded materiel was to be recycled, given away, or thrown away. We allocated two weeks to this step based on the assumption that we would continue to sort as we found more materiel during the second and third steps.
This was a very large task. Nearly a decade's worth of materiel was lying around the facility. The crew started by designating areas for materiel based on its destination. Areas were marked for landfill materiel, recyclables and metals, hazardous waste products, and materiel to be returned to the supply system. Dumpsters were ordered for the landfill materiel, and sites were prepared for hazardous materials handling and shipment.
During this step, four 40-cubic-yard dumpsters of cement debris, nonrecyclable plastics, and rotting wood were taken to the landfill. About 30,000 pounds of scrap metal was recycled. About 300 gallons of hazardous waste was removed. About 100 used light bulbs containing mercury vapors were removed. Salvageable wood was set aside and stacked according to dimensions and grade. The shipping containers were emptied.
SET IN ORDER. Shipping containers were assigned for each of the major items--construction and grounds tools, expendable and seasonal items, doors and windows, bulk construction materiel, plumbing and electrical goods, and repair parts. Containers were organized using shelves and dividers. Hazardous products were placed in fireproof lockers.
Materiel in the lay down yards was staged in groups of like materiel. For example, red metal siding was placed with red metal corners and trim. Commonly used materiel was placed toward the front of the lay down areas while materiel not often used was placed at the back.
As the lay down yards were organized, we recognized the need for shelter for some materiel and began requesting approval to erect a permanent cover. Once the permanent cover was in place, shelves were installed to reduce the size of the lay down area and the related congestion. This reduced materiel damage.
During this process more unneeded materiel was found. Redundancies in materiel were noted and lost materiel was recovered. Stockpiled expensive building materiel was stored until ready for use. The facility manager's office inventoried all materiel. A map of the containers and lay down yard is on display in the office.
SHINE. The shine step came easily. After discarding or recycling most of the materiel, it was easy to get in and clean house. By this time, the Soldiers were actually excited about it. They saw what their hard work was starting to create and did not need much motivation to get out and clean the facility.
STANDARDIZE. In this step, we created individual kits for common tasks. Tools were placed in bags or boxes related to a specific task. Standardizing the kits was a very practical approach. It had already proved itself as a great time saver when preparing for common tasks.
An example of a kit we designed is the environmental control unit kit. We knew from experience that we had power surges at the forward operating base where the students slept. These surges caused the air conditioners to start simultaneously, creating a voltage drop that blew the start capacitors.
To replace a capacitor, the mechanic needed a new capacitor, a jumper wire, a testing stick, and replacement screws. We combined these items in a tool bag, which reduced the need to search for each item individually before starting the repair. It also allowed us to stage a few of these kits near the sleep tents, making them easily accessible.
The tool bags helped in expediting repairs and ensure mechanics use the proper tools. The Soldiers worked on a training system and standard operating procedures for common repairs. Once finished, they will be published so that all tasks are completed to the same standard.
The eight containers were also standardized by placing the lights in similar locations, keeping brooms and dustpans just inside the doors, and posting inventory lists inside the doors. When possible, all containers were organized with a common theme of item placement.
SUSTAIN. To sustain our efforts, we created site maps for each area. Pictures were taken of each site and posted to show the Soldiers how the areas should look daily. This gave the Soldiers a model. The intent was to establish self-sufficiency by educating the Soldiers and indoctrinating them in the process. The goal was to empower the Soldiers to keep up the process and to continue to improve.
Excess materiel is inventoried and used before more of the same product is ordered. The facility manager established a database of stock numbers based on historical and projected use. In an effort to cut down on the habit of storing items "just in case," no space has been allocated for unusable materiel.
Materiel ordered commercially is now assigned a purchase order number associated with a specific building project. The materiel is stored on the building site. This has reduced multiple movements of the same freight. It has also reduced the amount of the misplaced materiel. The C Company commander periodically inspects the areas to ensure the standards are met.
The application of Lean manufacturing principles and 5S has transformed the process of facility maintenance and project management for C Company. The process has saved the Army money, labor, and resources.
The transformation has been an eye-opening experience that has caused ripple effects in the company's efficiency and in its training mission. Soldiers are faster and more accurate when dealing with problems, and attitudes are improved. C Company is providing a better quality product for its customers through the implementation of Lean manufacturing principles and 5S.
__________________________________________________________________________________________
Capt. Adam E. Stickley is assigned to the John F. Kennedy Special Warfare Center and School at Fort Bragg, N.C., as the executive officer and facility manager of the Freedom Training Facility. He holds a bachelor's degree in technology education and a master's degree in industrial technologies from the University of Central Missouri. He is enrolled in the International Facility Management Association's facility management credentialing program.
__________________________________________________________________________________________
This article was published in the May-June 2013 issue of Army Sustainment magazine.
Related Links:
Browse Army Sustainment Magazine
Social Sharing